hootrpootr
Aerospace
Hello, I’m trying to determine what the shear and moment diagrams of a bolt in single shear look like. Before anyone says it, I know that it’s rare that a bolt will ever fail first in bending, and this is something that typically isn’t even checked for.
Anyway, I’ve assumed that the bolt is essentially a beam cantilevered at one end and guided at the other (guided end only allows vertical translation, no rotation). I’ve applied a distributed load acting downward over half the bolt length, and a distributed load acting upward over the other half. I found a website that uses these assumptions as well, and even provides a shear diagram (I’ve arrived at the same conclusion). Does the moment diagram match the drawing I’ve attached?
Website (see figure 4.2.4):
Thanks!
Anyway, I’ve assumed that the bolt is essentially a beam cantilevered at one end and guided at the other (guided end only allows vertical translation, no rotation). I’ve applied a distributed load acting downward over half the bolt length, and a distributed load acting upward over the other half. I found a website that uses these assumptions as well, and even provides a shear diagram (I’ve arrived at the same conclusion). Does the moment diagram match the drawing I’ve attached?
Website (see figure 4.2.4):
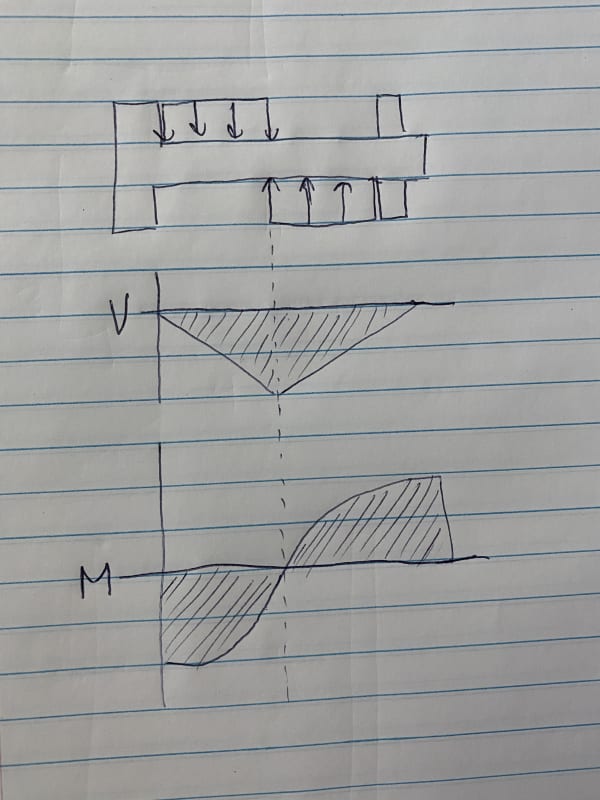
Thanks!