Drej
Mechanical
- Jul 31, 2002
- 971
I've spent many an hour trawling through articles and codes, searching through old posts on here, and just generally searching on Google without really bottoming this out.
Assume there is a requirement to join a length of Square Hollow Section (say, 80x80x5) to a smaller SHS (say, 40x40x5) by welding, such that the smaller section sits on its end perpendicular to the larger section (see detail below). What is the maximum size* fillet weld that can be made assuming only a single-sided fillet weld on the periphery of the smaller SHS?
The various guidance (and sometimes opinion) appears to be that the "maximum size" of the fillet weld is related to the thickness/es of the sections being joined. However, given this guidance, from a design strength (calculation) standpoint the weld will not be as strong as the section (which is also a requirement). To achieve this, I would need to increase the weld size.
If you match the weld size to the section thickness, from a design strength standpoint the weld will always be of lower relative strength. My interpretation of the guidance is that the max fillet weld size is there to ensure the weld itself will be able to fully transfer the load between members, but the weld is still lower in design strength capacity relative to the section.
In summary, my understanding isn't clear. Can I simply increase the size of the fillet weld to gain the required increased strength from a calculation standpoint, or are the max size guidelines in place to ensure we avoid secondary problems with over-sized welds such as distortion, cracking, residual stresses, etc.?
Any insight appreciated. Thanks.
*Leg length
------------
See faq569-1083 for details on how to make best use of Eng-Tips.com
Assume there is a requirement to join a length of Square Hollow Section (say, 80x80x5) to a smaller SHS (say, 40x40x5) by welding, such that the smaller section sits on its end perpendicular to the larger section (see detail below). What is the maximum size* fillet weld that can be made assuming only a single-sided fillet weld on the periphery of the smaller SHS?
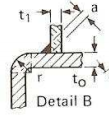
The various guidance (and sometimes opinion) appears to be that the "maximum size" of the fillet weld is related to the thickness/es of the sections being joined. However, given this guidance, from a design strength (calculation) standpoint the weld will not be as strong as the section (which is also a requirement). To achieve this, I would need to increase the weld size.
If you match the weld size to the section thickness, from a design strength standpoint the weld will always be of lower relative strength. My interpretation of the guidance is that the max fillet weld size is there to ensure the weld itself will be able to fully transfer the load between members, but the weld is still lower in design strength capacity relative to the section.
In summary, my understanding isn't clear. Can I simply increase the size of the fillet weld to gain the required increased strength from a calculation standpoint, or are the max size guidelines in place to ensure we avoid secondary problems with over-sized welds such as distortion, cracking, residual stresses, etc.?
Any insight appreciated. Thanks.
*Leg length
------------
See faq569-1083 for details on how to make best use of Eng-Tips.com