Hi, I am trying to realise sinusoidal motion of my tool and at the same time, my tool is vibrating elliptically.
Right now, I am using Displacement on the reference point of my tool, initial step all 0, step 1 allow X and Y to move.
For the vibration of the tool, I use Velocity with Periodic Amplitude for X and Y respectively.
I input values for amplitude, and I gave a initial speed for X direction to allow forward motion by giving a value for initial amplitude in the Periodic amplitude. For Y direction, I enter 0 for initial amplitude.
(Because in Periodic Amplitude, initial amplitude= initial speed)
However, in order to realise sinusoidal motion of the tool, I cannot give a value for initial amplitude of Y direction, as it will go only one way, which is not what I want as sinusoidal motion requires up and down motion in Y direction.
I thought of using subroutines but there is no subroutines available for Velocity.
Actually I was told that I can realise this motion without using subroutines, and I have seen ax example of a 2D simulation of elliptical vibration cutting in sinusoidal motion.
It would be great if someone could provide some advice. Thank you.
Right now, I am using Displacement on the reference point of my tool, initial step all 0, step 1 allow X and Y to move.
For the vibration of the tool, I use Velocity with Periodic Amplitude for X and Y respectively.
I input values for amplitude, and I gave a initial speed for X direction to allow forward motion by giving a value for initial amplitude in the Periodic amplitude. For Y direction, I enter 0 for initial amplitude.
(Because in Periodic Amplitude, initial amplitude= initial speed)
However, in order to realise sinusoidal motion of the tool, I cannot give a value for initial amplitude of Y direction, as it will go only one way, which is not what I want as sinusoidal motion requires up and down motion in Y direction.
I thought of using subroutines but there is no subroutines available for Velocity.
Actually I was told that I can realise this motion without using subroutines, and I have seen ax example of a 2D simulation of elliptical vibration cutting in sinusoidal motion.
It would be great if someone could provide some advice. Thank you.
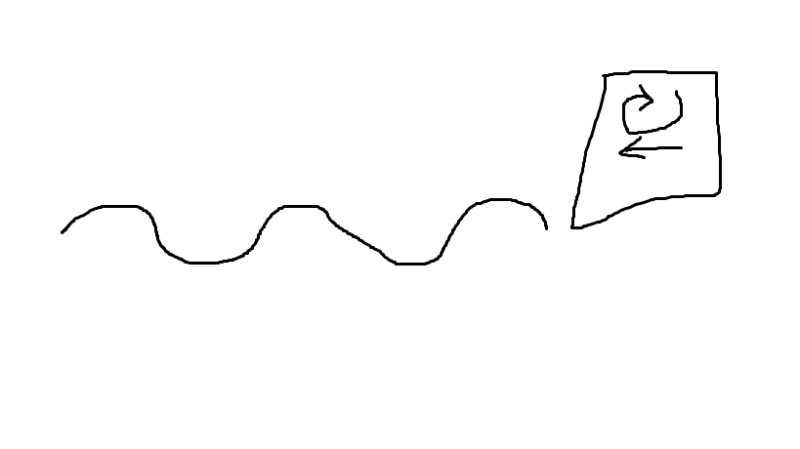