EloyRD
Mechanical
- Jan 31, 2013
- 33
Hi,
I'd like some opinions about guaranteeing easiness of operation of a siphon connecting two ponds.
The installation is at sea level for irrigation, the configuration is:
- there is an existing pond of 600,000-cubic-meters of water capacity and 8-meters of water depth. This existing pond has a pumping station of up to 5.2 m3/s and is fed by a 5.6 m3/s open channel.
- my civil engineering colleagues have designed a 1,800,000-cubic-meters pond with the same elevations for bottom and crown of the pond. The design intention is that the new pond increases the water-storage-capacity of the system.
I'm analyzing the mechanism to connect the two ponds. I'm proposing a siphon with piping, a priming valve and air valve at the top of the pipe, and two valves at the bottom of each pond.
My doubts are the following, and I will appreciate any comment about them:
- I am expecting that after priming the system, the two ponds will try to maintain the same water level, with the flow going in one direction or forward as required. Does it works that way?
- Is there a way to operate the submerged mechanical-valves from the surface that isn't an electrical actuator?
- Are regular air valves (like ARI) what I need for this application? I found nothing on their website regarding operation when the water in the inside is below air pressure
Thanks for any opinion.
I'd like some opinions about guaranteeing easiness of operation of a siphon connecting two ponds.
The installation is at sea level for irrigation, the configuration is:
- there is an existing pond of 600,000-cubic-meters of water capacity and 8-meters of water depth. This existing pond has a pumping station of up to 5.2 m3/s and is fed by a 5.6 m3/s open channel.
- my civil engineering colleagues have designed a 1,800,000-cubic-meters pond with the same elevations for bottom and crown of the pond. The design intention is that the new pond increases the water-storage-capacity of the system.
I'm analyzing the mechanism to connect the two ponds. I'm proposing a siphon with piping, a priming valve and air valve at the top of the pipe, and two valves at the bottom of each pond.
My doubts are the following, and I will appreciate any comment about them:
- I am expecting that after priming the system, the two ponds will try to maintain the same water level, with the flow going in one direction or forward as required. Does it works that way?
- Is there a way to operate the submerged mechanical-valves from the surface that isn't an electrical actuator?
- Are regular air valves (like ARI) what I need for this application? I found nothing on their website regarding operation when the water in the inside is below air pressure
Thanks for any opinion.
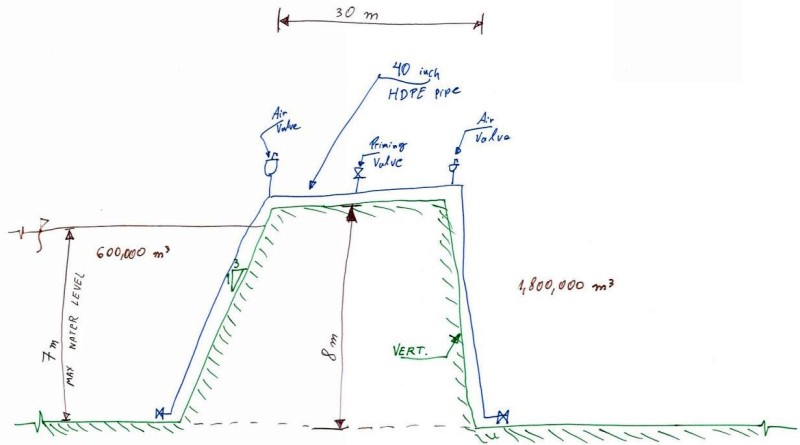