Hello guys,
I have struggle with acceptance criteria for hole, you can check dimensions on picture and calculation.
Through calculation I can see that for hole diameter of 10.2 mm I get bonus tolerance for position to 0.7 mm, by rule when I get bonus tolerance it means that I get increased positional tolerance but I increase also the size of the hole. Which means that I can accept hole with diameter of 10.9 mm in this case (10.2 + 0.7 = 10.9 mm).
With calculation I can see that end result with biggest bonus tolerance of 1 mm I can accept hole with diameter of 11.5 mm, did I understand this or I misunderstand something?
I have struggle with acceptance criteria for hole, you can check dimensions on picture and calculation.
Through calculation I can see that for hole diameter of 10.2 mm I get bonus tolerance for position to 0.7 mm, by rule when I get bonus tolerance it means that I get increased positional tolerance but I increase also the size of the hole. Which means that I can accept hole with diameter of 10.9 mm in this case (10.2 + 0.7 = 10.9 mm).
With calculation I can see that end result with biggest bonus tolerance of 1 mm I can accept hole with diameter of 11.5 mm, did I understand this or I misunderstand something?
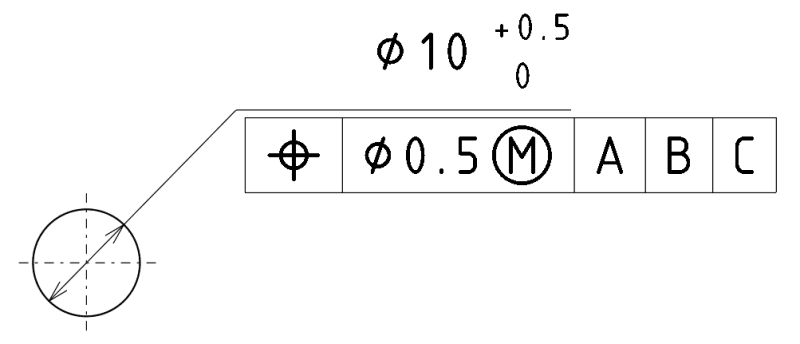
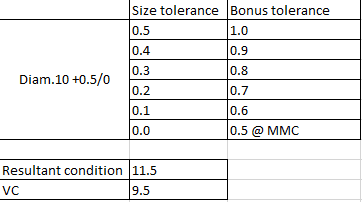