Hi All,
I am modeling a steel joist in RISA and I am curious about what is the correct and/or permissible way to analyze the top chord for bending moments. What I mean by that is that if I model the joist as a whole I am getting different moments for the top chord than if I would model the top chord as an independent fully supported continuous member. The difference is substantial as you can see from this screen shot.
The top diagram is just the top chord as a continuously supported member. The bottom diagram is the chord as part of the entire joist. Which way are you guys using to determine the required bending in your top chords?
Thank you!
I am modeling a steel joist in RISA and I am curious about what is the correct and/or permissible way to analyze the top chord for bending moments. What I mean by that is that if I model the joist as a whole I am getting different moments for the top chord than if I would model the top chord as an independent fully supported continuous member. The difference is substantial as you can see from this screen shot.
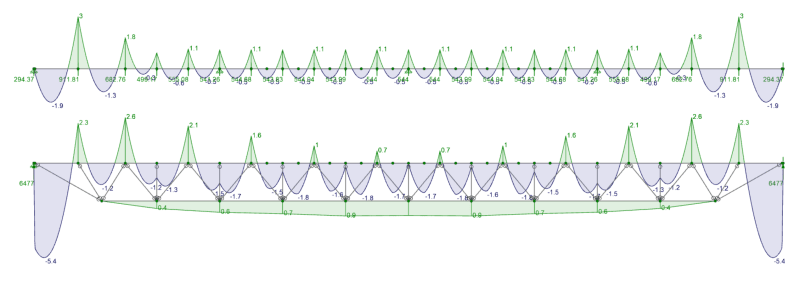
The top diagram is just the top chord as a continuously supported member. The bottom diagram is the chord as part of the entire joist. Which way are you guys using to determine the required bending in your top chords?
Thank you!