jpaero
Aerospace
- Dec 14, 2007
- 24
I have a structure similar to the one shown below. The structure was originally analyzed using FEA with Rib(A) present. Due to some issue, we need to ignore the presence of Rib (A). We are not in a position to re-run the FEM. We have the panel shear flows for each of the panels based on the original FEA. Since the rib became ineffective, the panel dimensions now change from 20" x 40" (Bay 1) and 30" x 40" (Bay 2) to being 50" x 40" (Bay 1+2). Each panel had shear flows q1, q2 and q3 based on the original FEA. I am unable to clear the combined panel for the max. shear when checking for shear buckling and I am looking for ways to remove conservatism. Can I assume the effective shear in the combined panel 1 & 2 to be (q1 x 20" + q2 x 30")/(20"+30")? I have seen this kind of averaging being done for panels along a cross-section but not so sure if I can do it along a span.
Also if possible, provide references for your answers.
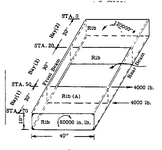
Also if possible, provide references for your answers.
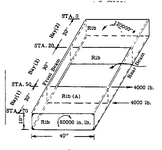