Hello, I am currently designing a test rig to test high speed carbon bows. I recently hit a snag when I was told to add a slip ring to the design. Anyone have any ideas or tips on how I should integrate this into the design? The slip rig has to withstand up to 4000rpm so I have selected the g012-12 Sereis. Pictures attached. Thank you!
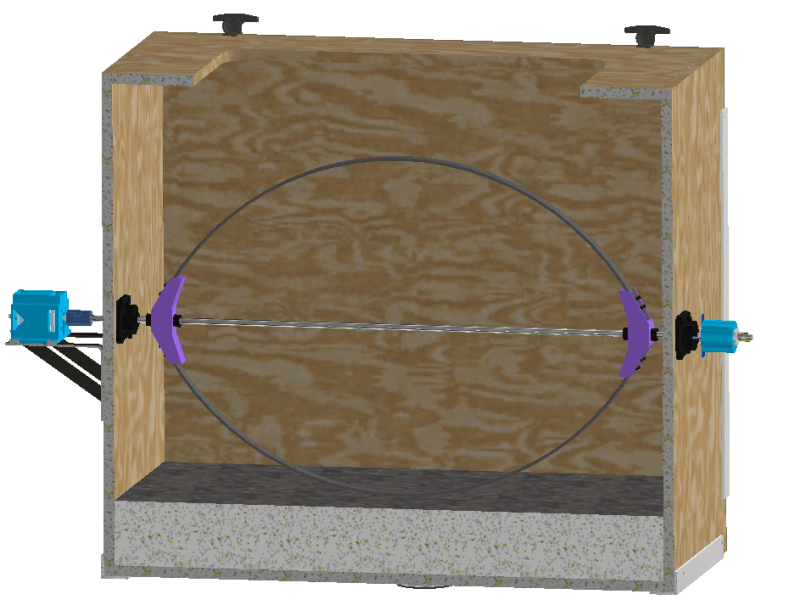
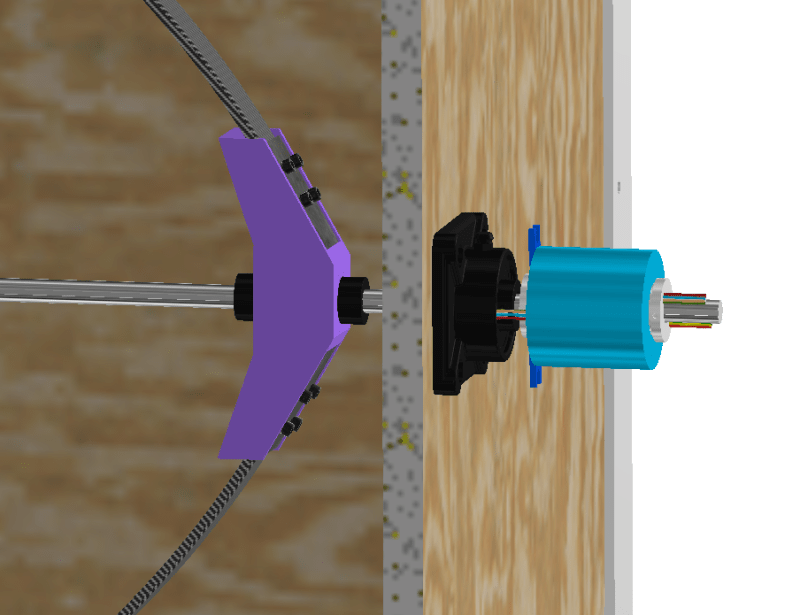
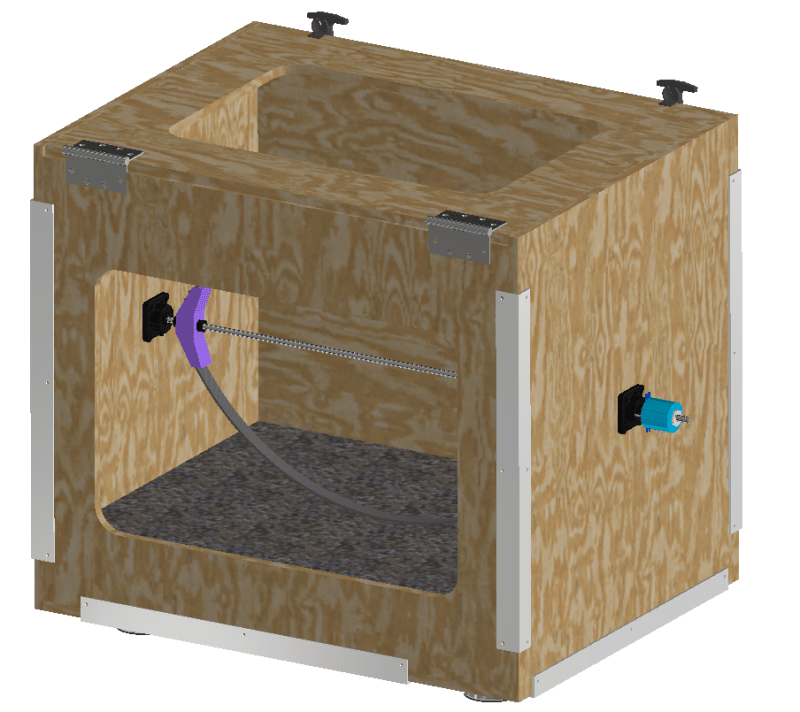