qubitsized
Civil/Environmental
Hi everyone!
We have a 15 bar progressive cavity pump that is conveying lime-treated sludge to an 8-m high, 4-mΦ cylindrical concrete silo at the rate of 5 m3/h. We decided to inject the sludge cake at the bottom of the silo instead of the top as shown below:
Diameter of conveying stainless pipe is 150mm, sludge cake density is 1070 kg/m3. Conveying distance is ~5.0m.
Will this work?
We have a 15 bar progressive cavity pump that is conveying lime-treated sludge to an 8-m high, 4-mΦ cylindrical concrete silo at the rate of 5 m3/h. We decided to inject the sludge cake at the bottom of the silo instead of the top as shown below:
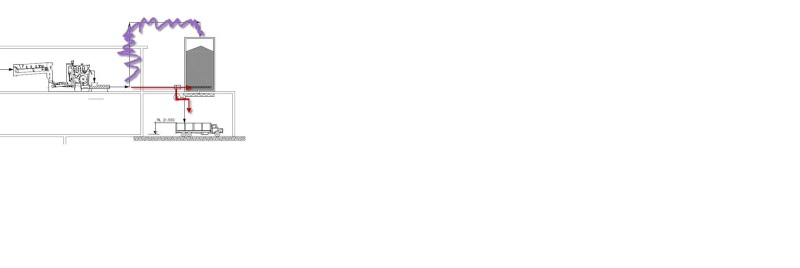
Diameter of conveying stainless pipe is 150mm, sludge cake density is 1070 kg/m3. Conveying distance is ~5.0m.
Will this work?