jacksonfem
Structural
Hello,
I have a model with solid elements, simulating a clip, as you can see in the image below. In SOL 601, with NxNastran, I can easily simulate the male clip moving out from the female and in again with a transient analysis, as you can see in the images sequence. But when I try to perform the same simulation is MscNastran's SOL 400, the solver cannot find convergence and stops. The non-convergence begin when the 2 bodies are in contact. I really can 't find why. I don 't use any special contact parameters in SOL 601. Just the defaults.
In SOL 400 I use adaptive time stepping and not fixed, just like in SOL 601.
Do you have any idea of what is happening?
I have a model with solid elements, simulating a clip, as you can see in the image below. In SOL 601, with NxNastran, I can easily simulate the male clip moving out from the female and in again with a transient analysis, as you can see in the images sequence. But when I try to perform the same simulation is MscNastran's SOL 400, the solver cannot find convergence and stops. The non-convergence begin when the 2 bodies are in contact. I really can 't find why. I don 't use any special contact parameters in SOL 601. Just the defaults.
In SOL 400 I use adaptive time stepping and not fixed, just like in SOL 601.
Do you have any idea of what is happening?

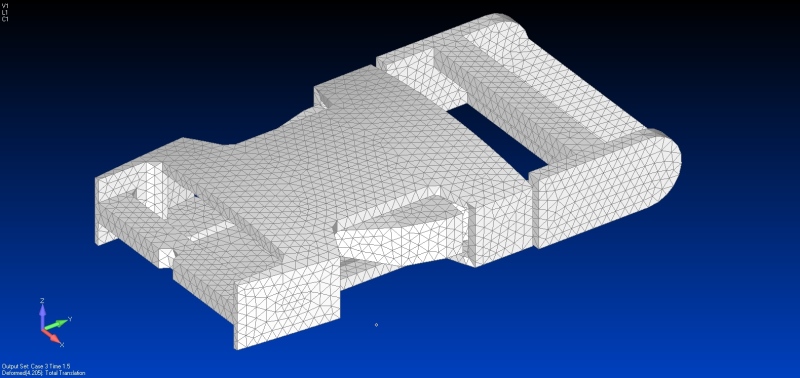
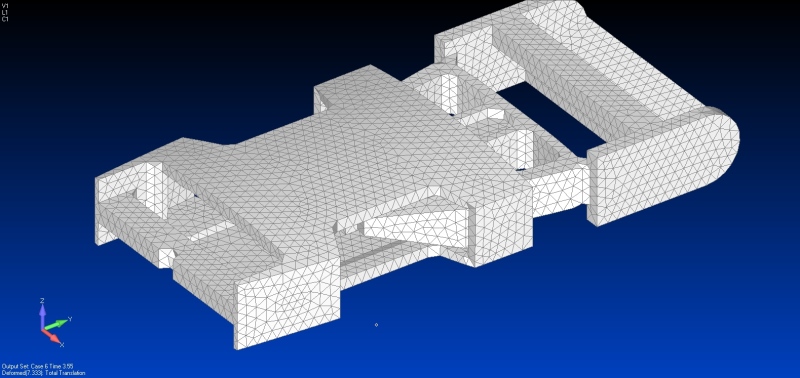
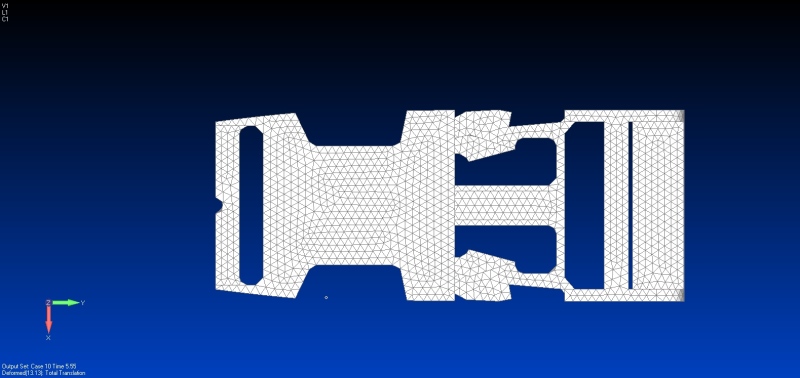
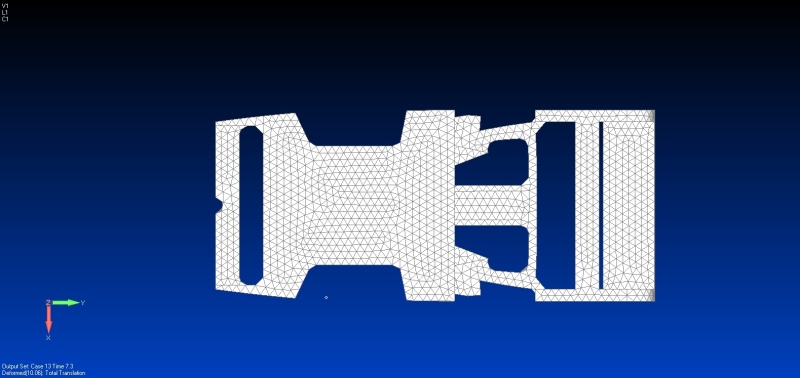
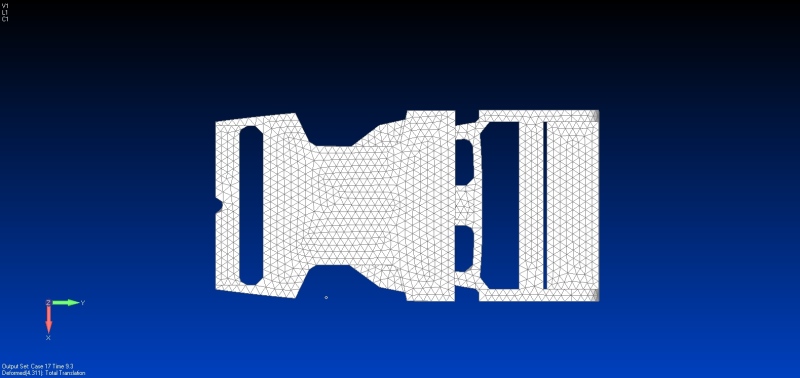
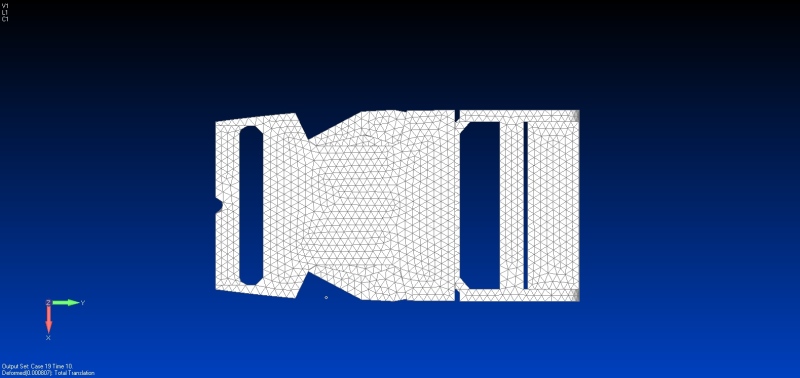