JuruteraWA
Petroleum
- Mar 25, 2022
- 2
Greetings,
I have a set of solenoid valves that need 24V +/- 10% to operate properly. Unfortunately, my PLC is about 1000' away (with existing 16 gauge wires). My electric circuits is a little rusty. Will the following diagram work with the voltage requirements at the solenoids? Seems like it would if I put the power supply close to the solenoid. But I'm not sure how that 1000' to the PLC on the "-" side will affect the voltage.
Option B would be to use an interposing relay. I'm hoping to avoid if possible (this is a SIF and would prefer to not add components to affect the achieved SIL). Any input would be much appreciated. Thank you!
I have a set of solenoid valves that need 24V +/- 10% to operate properly. Unfortunately, my PLC is about 1000' away (with existing 16 gauge wires). My electric circuits is a little rusty. Will the following diagram work with the voltage requirements at the solenoids? Seems like it would if I put the power supply close to the solenoid. But I'm not sure how that 1000' to the PLC on the "-" side will affect the voltage.
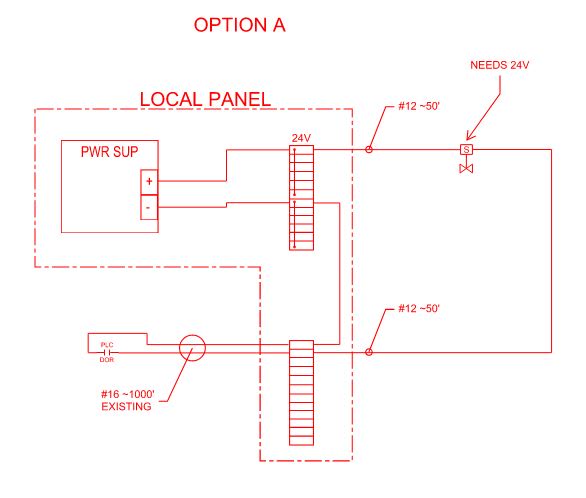
Option B would be to use an interposing relay. I'm hoping to avoid if possible (this is a SIF and would prefer to not add components to affect the achieved SIL). Any input would be much appreciated. Thank you!