Hi all,
I run a FEA on an assembly and I am not sure if I can trust my results or if they are "polluted" by a singularity.
The top part, a gearbox generate a torque transmitted through some bolts an pins connectors to the folded parts, the Mounting Box. (Enclosed "Gearbox connection")
This mounting box is connected to a fixed body thanks to a pin connector and some 3D bolts. (Enclosed "Body connection")
My assumption is that the gearbox connection is rigid when the body connection can allow some movement under the bolts if the bolt preload is too low.
I applied a force on the top of the bolt to model the preload and I set a friction of 0.1 between the bolt head and the Mounting Box and between the Mounting box and the body.
The assembly seams to deform as expected, when increasing the torque I can see some movement under the bolt until the box hit the bolt diameter.
My problem is that I get very high stresses on the corner of the mounting box and I am wondering if I should worry about it.
I believe my simulation allow me to correctly plot the displacement but that the stress isn't accurate because of this singularity.
How can I get correct reading of the maximum stress in this corner?
I tried simplifying the model by only keeping the mounting Box and I don't have at all the same kind of stress.
Any though about my results?
Thanks a lot.
Gearboxe connection
Body connection
Deformation
Stress concentration / singularity
I run a FEA on an assembly and I am not sure if I can trust my results or if they are "polluted" by a singularity.
The top part, a gearbox generate a torque transmitted through some bolts an pins connectors to the folded parts, the Mounting Box. (Enclosed "Gearbox connection")
This mounting box is connected to a fixed body thanks to a pin connector and some 3D bolts. (Enclosed "Body connection")
My assumption is that the gearbox connection is rigid when the body connection can allow some movement under the bolts if the bolt preload is too low.
I applied a force on the top of the bolt to model the preload and I set a friction of 0.1 between the bolt head and the Mounting Box and between the Mounting box and the body.
The assembly seams to deform as expected, when increasing the torque I can see some movement under the bolt until the box hit the bolt diameter.
My problem is that I get very high stresses on the corner of the mounting box and I am wondering if I should worry about it.
I believe my simulation allow me to correctly plot the displacement but that the stress isn't accurate because of this singularity.
How can I get correct reading of the maximum stress in this corner?
I tried simplifying the model by only keeping the mounting Box and I don't have at all the same kind of stress.
Any though about my results?
Thanks a lot.
Gearboxe connection
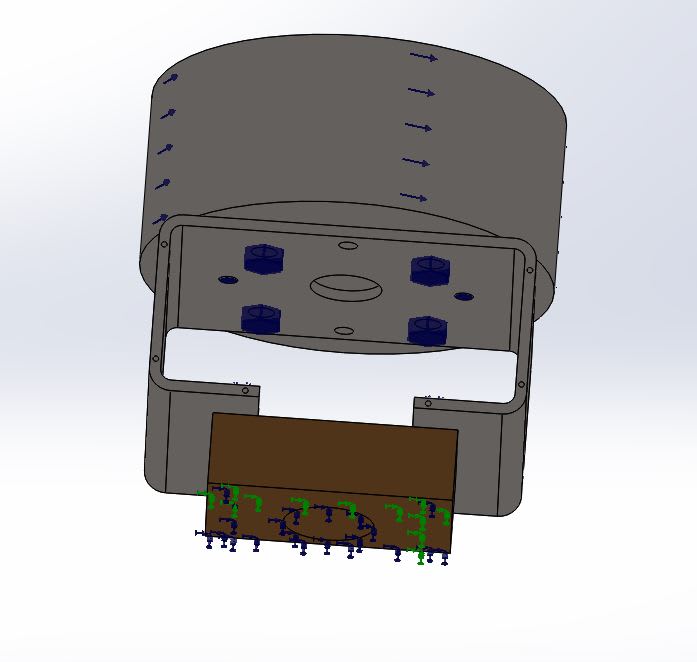
Body connection
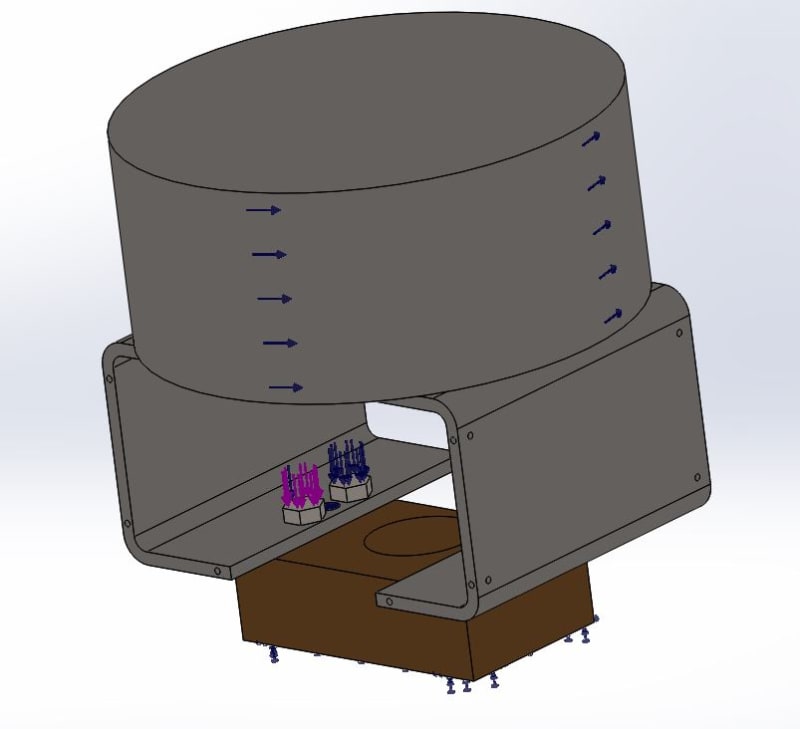
Deformation
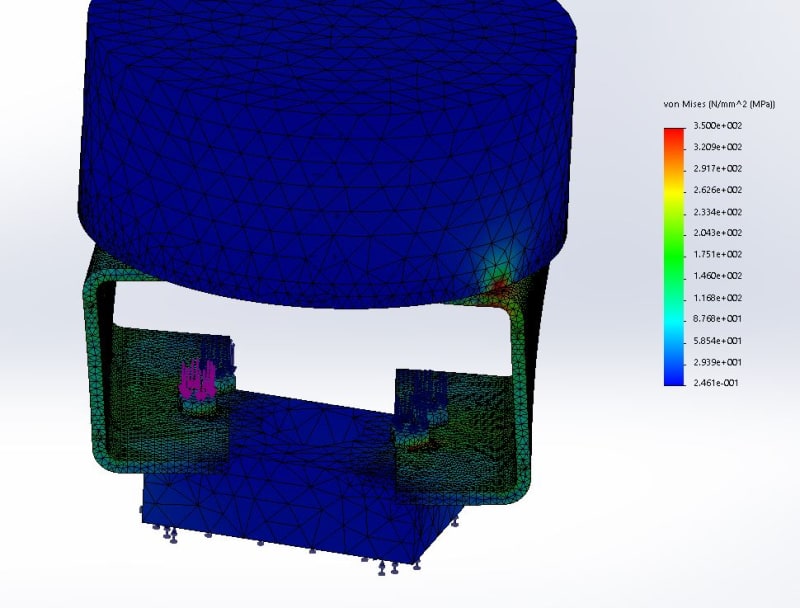
Stress concentration / singularity
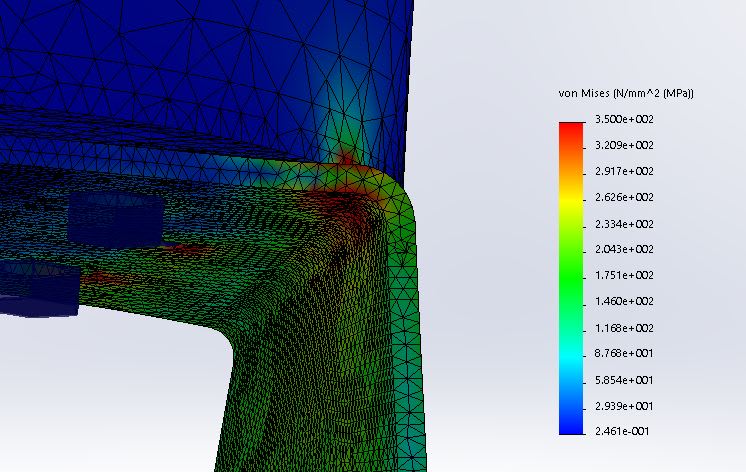