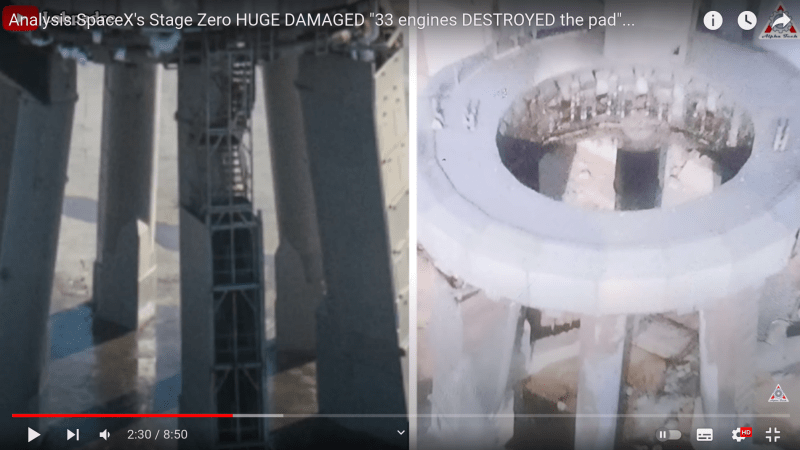
The above photo was from a youtube video showing the reinforced concrete supporting structure of the SpaceX rocket before and after the yesterday's launch when it exploded 4 minutes into the flight.
It appears the RC slab was flush as one level prior to the launch but now has the ground beams exposed. The video also claimed there were concrete fragments flying all over the place as shrapnel damaging some fuel and water tanks.
There seem to be at least the following issues in play:-
(1) The "disappeared" reinforced concrete slab was totally unsuitable for its purpose. I do not know if it was reinforced or not but it would have been criminal if it wasn't.
(2) The reinforced concrete columns and ground beams show little damage. This would suggest the reinforced concrete in adequate dimension could be the suitable material for the structure including the slab if adequately shield from the high temperature heat.
(3) Had any of the RC column or ground beam failed during the last launch the supporting structure might not have remained static then the rocket could have shot off at an angle other than vertically upward. Consequently a huge disaster could occur if the rocket hit the population with the amount of fuel it carried.