MitchusMaximus
Electrical
Hi, all. I work in VFD and electrical controls sales, and I have a customer who is looking to apply some faster braking to his VFD driven motor when he is balancing straw choppers. We are driving a 40HP 1725 rpm motor, being run at a top speed of 1294 rpm. He did some experiments and recorded the time to decelerate the the load as about 30s from the top speed. The worst case duty cycle the resistor would deal with is 10s/85s (acceleration, run time, deceleration time, and rest time adding up to 85s, decelerating for 10s at the longest.) or around 12%. I've run across some application notes on sizing the power rating of your resistor based on the braking torque needed and the braking duty cycle, but I am missing a crucial piece of information to work that out, that being the moment of inertia of the load. I believe the mass of the chopping assembly is about 200kg, but I don't know to work out the moment of inertia for such an irregular shape (see attached images for examples).
Can I manipulate some physics formulas with what I have given and come up with an estimated value for a moment of inertia, based on my angular deceleration? Or is this just something I can't theorize my way out of and I need to get their mechanical guys to figure out?
We are also using a braking unit that has a minimum braking resistor value of 4Ω, and the motor is rated at 230VAC.
Cheers
Can I manipulate some physics formulas with what I have given and come up with an estimated value for a moment of inertia, based on my angular deceleration? Or is this just something I can't theorize my way out of and I need to get their mechanical guys to figure out?
We are also using a braking unit that has a minimum braking resistor value of 4Ω, and the motor is rated at 230VAC.
Cheers
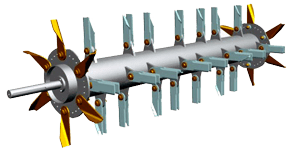
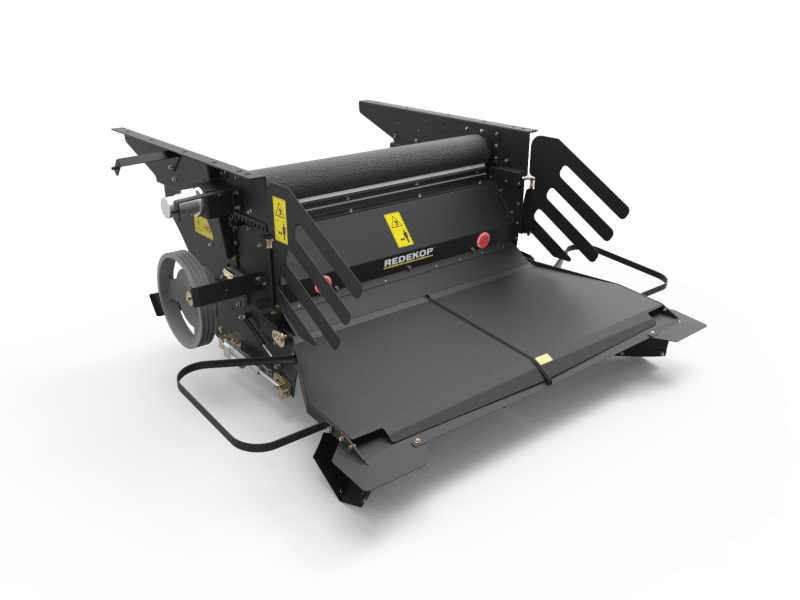