Hello,
First time poster -- hopefully I'm posting in the right place and following forum rules. Please let me know otherwise.
I was tasked with spec'ing check valves for a boiler chemical injection system. My conceptual understanding of the fluid properties is a bit rusty, so I'd appreciate any insight.
* Metering pumps (~0.005 GPM) are on the second floor of the building, elevation 139 ft
* The chemical injection point is 30 ft below the pumps.
* The pipe at which it discharges into draws upwards of 120 GPM from a deaerator, and it's pumps are located in the basement, ~46 ft below the metering pumps.
* A single 50 psi cracking pressure check valve is installed immediately after the metering pumps on the second floor.
My task is to install two check valves after the metering pumps, and properly spec them to prevent siphoning of chemicals.
I have attached a sketch. Boiler chemical pump is the blue line, and the boiler feed water is the green pipe. The deaerator feed pumps are in orange. The labeled pressures were recorded off of actual pressure gauges. Flows were approximated. Pumps are in parallel.
My rational for spec'ing the check valves was to sum all of the suction forces after the metering pumps to the lowest point. From pumps to basement is a free-fall drop of 46 feet, equivalent to 20 PSI water column. I do not know how to estimate the effect of suction from the pumps in the basement on this system--I'm not sure if it is negligible or not.
My hunch is that check valves with a cracking pressure of 25 PSI should be satisfactory for this application, rather than the 50 PSI cracking pressure check valve that was previously installed.
Can anyone offer any input on this scenario? How could I best choose two check valves to install in series to ensure that boiler chemicals on the 2nd floor of a building are not siphoned throughout the system (minding the effects of hydrostatics/dynamics in this particular case)?
Thank you
First time poster -- hopefully I'm posting in the right place and following forum rules. Please let me know otherwise.
I was tasked with spec'ing check valves for a boiler chemical injection system. My conceptual understanding of the fluid properties is a bit rusty, so I'd appreciate any insight.
* Metering pumps (~0.005 GPM) are on the second floor of the building, elevation 139 ft
* The chemical injection point is 30 ft below the pumps.
* The pipe at which it discharges into draws upwards of 120 GPM from a deaerator, and it's pumps are located in the basement, ~46 ft below the metering pumps.
* A single 50 psi cracking pressure check valve is installed immediately after the metering pumps on the second floor.
My task is to install two check valves after the metering pumps, and properly spec them to prevent siphoning of chemicals.
I have attached a sketch. Boiler chemical pump is the blue line, and the boiler feed water is the green pipe. The deaerator feed pumps are in orange. The labeled pressures were recorded off of actual pressure gauges. Flows were approximated. Pumps are in parallel.
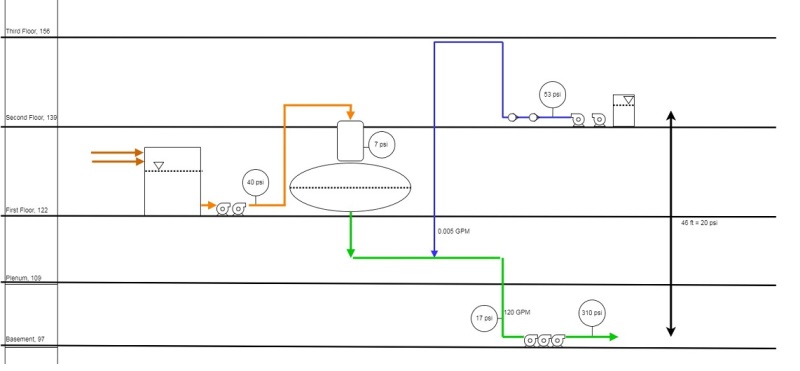
My rational for spec'ing the check valves was to sum all of the suction forces after the metering pumps to the lowest point. From pumps to basement is a free-fall drop of 46 feet, equivalent to 20 PSI water column. I do not know how to estimate the effect of suction from the pumps in the basement on this system--I'm not sure if it is negligible or not.
My hunch is that check valves with a cracking pressure of 25 PSI should be satisfactory for this application, rather than the 50 PSI cracking pressure check valve that was previously installed.
Can anyone offer any input on this scenario? How could I best choose two check valves to install in series to ensure that boiler chemicals on the 2nd floor of a building are not siphoned throughout the system (minding the effects of hydrostatics/dynamics in this particular case)?
Thank you