For mostly curiosity, but at this stage also the preservation of sanity, there is an ongoing discussion in our office on why we see weld on pad eyes/lifting lugs with splits in them. See image below:
We can speculate some minor decrease in certain stresses (e.g. contact stress reduction as it will more easily flex to conform to slightly lower radius of the pin inside it), but at the cost of large stress increases in other areas (bending stress in the eye, peak fatigue stress concentration for any longitudinal stresses in the plate to which it is welded to). It doesn't seem easier to weld (if anything it seems more difficult), and it doesn't seem cheaper to manufacture.
So we are generally at a loss.
My best guess is someone drew this 40 years ago by hand, sneezed near the end of the drawing process, left a line on the drawing, and went "Well, not drawing that again. Guess it's a feature now." and it never got corrected.
But realistically it's across multiple client sites, vendors, and industries. It's not common, but it exists everywhere. So there must be some reason this exists.
Can anyone try to illuminate me a little on this one?
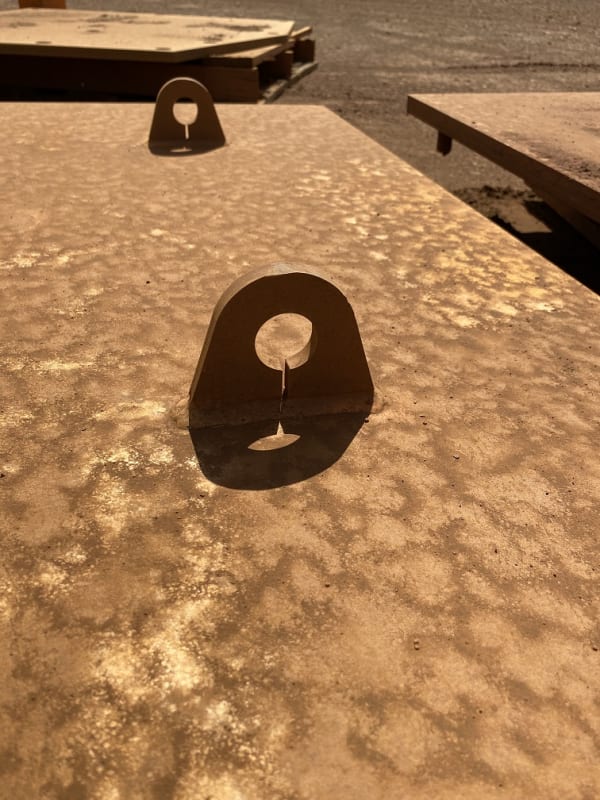
We can speculate some minor decrease in certain stresses (e.g. contact stress reduction as it will more easily flex to conform to slightly lower radius of the pin inside it), but at the cost of large stress increases in other areas (bending stress in the eye, peak fatigue stress concentration for any longitudinal stresses in the plate to which it is welded to). It doesn't seem easier to weld (if anything it seems more difficult), and it doesn't seem cheaper to manufacture.
So we are generally at a loss.
My best guess is someone drew this 40 years ago by hand, sneezed near the end of the drawing process, left a line on the drawing, and went "Well, not drawing that again. Guess it's a feature now." and it never got corrected.
But realistically it's across multiple client sites, vendors, and industries. It's not common, but it exists everywhere. So there must be some reason this exists.
Can anyone try to illuminate me a little on this one?