Jack Nicholson
Chemical
- Oct 20, 2016
- 119
Hi everyone!
In our C2 recovery plant, there is a Propane refrigerant cycle to lower the NG temperature.
In current state, the Anti-surge control valve (330-FV-015) is a little open, so we have to inject some low-temperature liquid propane to anti-surge line through (330-TV-001) to control and lower the suction drum compressors (330-V-3).
Surprisingly, the detailed engineer designed an injection nozzle without any spray nozzle!!!. Could you please help me out about how the designer didn't consider using any spray nozzle (like Full cone nozzles).
P.S.: Current operational parameters are as below and if we open 330-TV-001 more, the liquid propane would form in our suction drum. So we think that if we install a proper spray nozzle, we can open TV more and no liquid propane would be formed.
PID:
Operational Parameters:
Current liquid nozzle injection:
In our C2 recovery plant, there is a Propane refrigerant cycle to lower the NG temperature.
In current state, the Anti-surge control valve (330-FV-015) is a little open, so we have to inject some low-temperature liquid propane to anti-surge line through (330-TV-001) to control and lower the suction drum compressors (330-V-3).
Surprisingly, the detailed engineer designed an injection nozzle without any spray nozzle!!!. Could you please help me out about how the designer didn't consider using any spray nozzle (like Full cone nozzles).
P.S.: Current operational parameters are as below and if we open 330-TV-001 more, the liquid propane would form in our suction drum. So we think that if we install a proper spray nozzle, we can open TV more and no liquid propane would be formed.
PID:
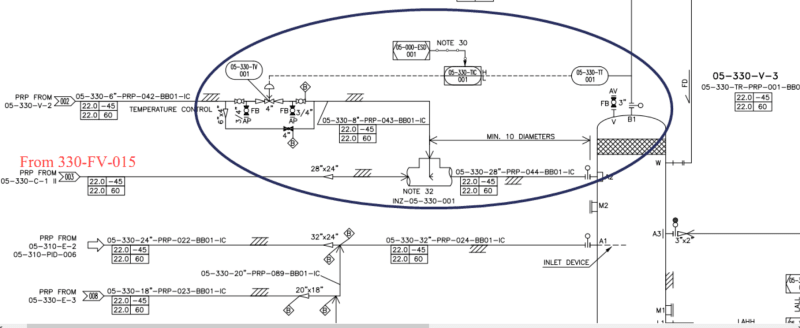
Operational Parameters:

Current liquid nozzle injection:
