durablack2
Automotive
I am curious if there would be any noticeable difference in feel or longevity of two different spring mounting systems.
On one end of the system we will have a moveable, range limited rod that mates up with a compression spring. The opposite end of the spring will mate to a fixed surface. The rod can move side to side and will always be in contact w/ the compression spring. The rod will have a handle protruding outwards (90 deg from axis) and will move by hand. Around 30 lbs of spring force at max compression, 10lbs at full extension. The rod will be enclosed in a cylindrical hole so it can only move back and forth in one direction.
I am wondering if either of the two types of mounting explained below will have any kind of difference. The reason I am asking is because type A will probably have more cost, but my colleague thinks it will allow for smoother operation.
Type A: Spring will be screwed onto a threaded boss of the rod, closed and ground end of fixed side
Type B: Spring will slip fit over the boss of the rod, closed and ground end on both sides
If Type A is better than B, could adding a washer between the rod and spring for type B improve smoothness when moving the rod? Other ideas?
Pic attached.
On one end of the system we will have a moveable, range limited rod that mates up with a compression spring. The opposite end of the spring will mate to a fixed surface. The rod can move side to side and will always be in contact w/ the compression spring. The rod will have a handle protruding outwards (90 deg from axis) and will move by hand. Around 30 lbs of spring force at max compression, 10lbs at full extension. The rod will be enclosed in a cylindrical hole so it can only move back and forth in one direction.
I am wondering if either of the two types of mounting explained below will have any kind of difference. The reason I am asking is because type A will probably have more cost, but my colleague thinks it will allow for smoother operation.
Type A: Spring will be screwed onto a threaded boss of the rod, closed and ground end of fixed side
Type B: Spring will slip fit over the boss of the rod, closed and ground end on both sides
If Type A is better than B, could adding a washer between the rod and spring for type B improve smoothness when moving the rod? Other ideas?
Pic attached.
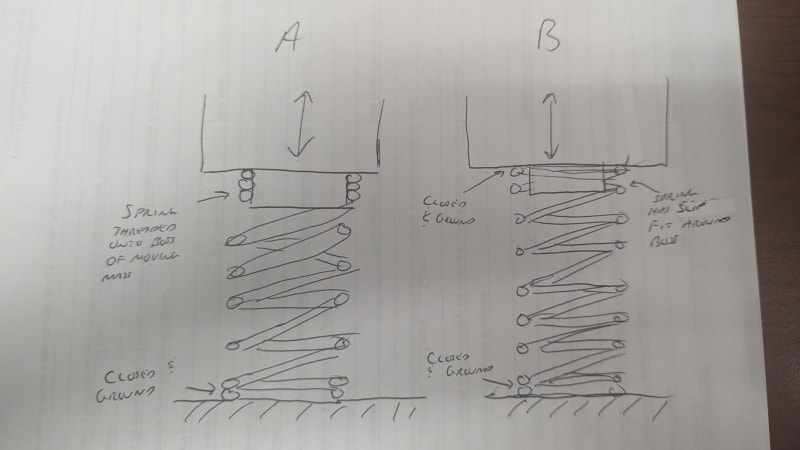