ModulusCT
Mechanical
- Nov 13, 2006
- 212
So nevermind what this says about our QA department that they've asked for a squareness tolerance on this assembly... I would however like to get some feedback regarding how best to tolerance this assembly. Please see the attached image. Below is the suggestion a senior engineer gave my drafter regarding how to control perpendicularity of the assembled frame. I suggested that this is over-toleranced, and redundant as controlling one centerplane with perpendicularity is appropriate, not the two centerplanes twice.
Below is my suggestion for making the frame square. What do you all think? Personally, I'm thinking that the peice parts should be toleranced correctly to control the assembly so this whole assembly tolerance thing is new to me, however, I'm new to this position and am trying to learn how best to process everyone's problematic drawings without throwing everyone into a state of disarray - you know, by following the Y14.5 standard.
Thanks in advance.
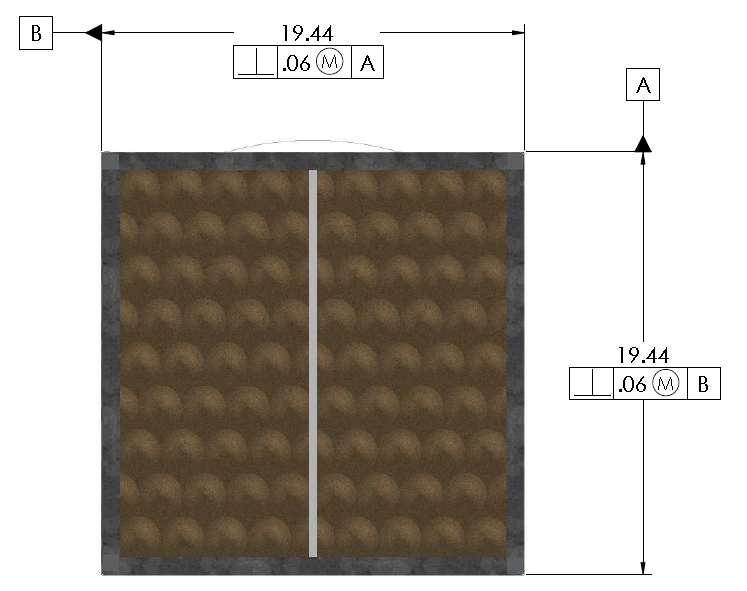
Below is my suggestion for making the frame square. What do you all think? Personally, I'm thinking that the peice parts should be toleranced correctly to control the assembly so this whole assembly tolerance thing is new to me, however, I'm new to this position and am trying to learn how best to process everyone's problematic drawings without throwing everyone into a state of disarray - you know, by following the Y14.5 standard.
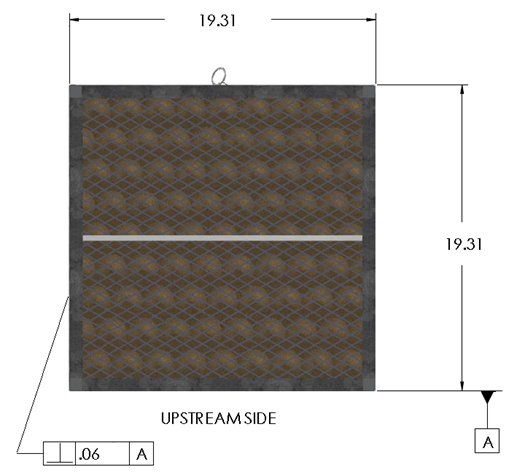
Thanks in advance.