AK4S
Structural
- Jan 2, 2015
- 98
I am looking at a new/proposed stair on an existing building which goes from a low roof to a High roof along a sloped roof portion. Its a maintenance stair (~3ft wide), so live load is limited (60psf snow load governs)
The stringer is lifted about 12" above the roof surface using a vertical post. The stringer is welded to the post, the post welded to the base creating a welded framed system. See sketch below:
I am trying to confirm if what I propose is stable. Do you see anything which might indicate an unstable condition?
IMO, the gravity load should go directly to the supporting post and there should not be an inclined component which goes along the stringer creating a condition where the stringer will slide down the roof? is that a correct interpretation?
As an option I could probably get better stability if I anchor the stringer directly on the low roof and eliminate the bottom-most post.
[Edit: The stair treads are welded to both stringers]
The stringer is lifted about 12" above the roof surface using a vertical post. The stringer is welded to the post, the post welded to the base creating a welded framed system. See sketch below:
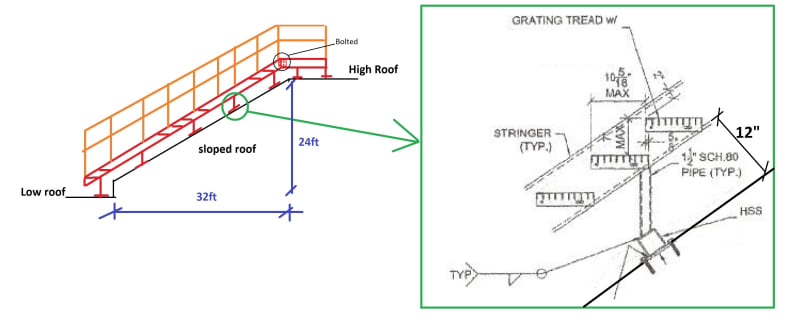
I am trying to confirm if what I propose is stable. Do you see anything which might indicate an unstable condition?
IMO, the gravity load should go directly to the supporting post and there should not be an inclined component which goes along the stringer creating a condition where the stringer will slide down the roof? is that a correct interpretation?
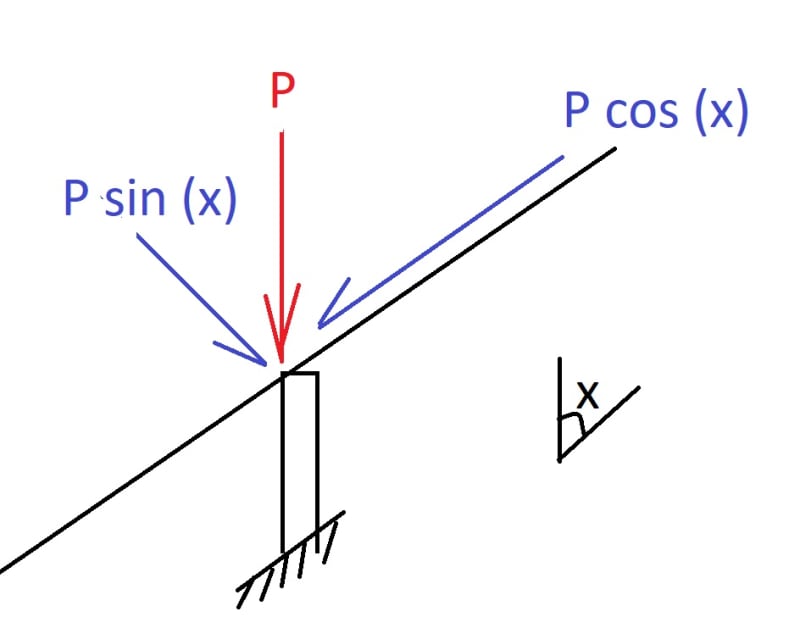
As an option I could probably get better stability if I anchor the stringer directly on the low roof and eliminate the bottom-most post.
[Edit: The stair treads are welded to both stringers]