Mannes Karsten
Petroleum
- Nov 16, 2017
- 14
Hi,
I'm unable to find a standard concerning rounded keys.
As seen by the image, the top part of the key is also rounded. Meaning the keyway in the hub has a rounded contour instead of a rectangular contour.
I'm reverse engineering a shaft with impellers that have these rounded keyways, but I need to know what the clearance should be between the hub and the top of the key and the rest of the standards.
Anyone got the golden tip?
I'm unable to find a standard concerning rounded keys.
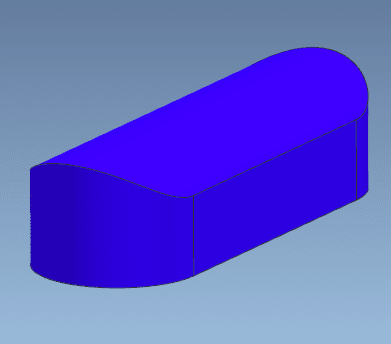
As seen by the image, the top part of the key is also rounded. Meaning the keyway in the hub has a rounded contour instead of a rectangular contour.
I'm reverse engineering a shaft with impellers that have these rounded keyways, but I need to know what the clearance should be between the hub and the top of the key and the rest of the standards.
Anyone got the golden tip?