I have some repairs that we are making to a steel plate girder bridge. We are welding new 1/4" steel plates to the outside of the girder web. We specified similar repairs to another area of this bridge last year and were told that the Contractor warped the 1/4" steel plates when they made the continuous CJP weld. Too much heat applied in one location all at once.
My question is this: Is there a difference in weld quality/strength if they were to weld continuously and completely around the web plate vs. stitch welding it 3" at a time @ 12" o.c. and then come back and weld in the areas to remain? In essence, does starting and stopping create issues at the point where you start/stop? They are most likely going to be using Shielded Metal Arc Welding but might choose to use flux cored arc welding too given the total length of the welds.
My question is this: Is there a difference in weld quality/strength if they were to weld continuously and completely around the web plate vs. stitch welding it 3" at a time @ 12" o.c. and then come back and weld in the areas to remain? In essence, does starting and stopping create issues at the point where you start/stop? They are most likely going to be using Shielded Metal Arc Welding but might choose to use flux cored arc welding too given the total length of the welds.
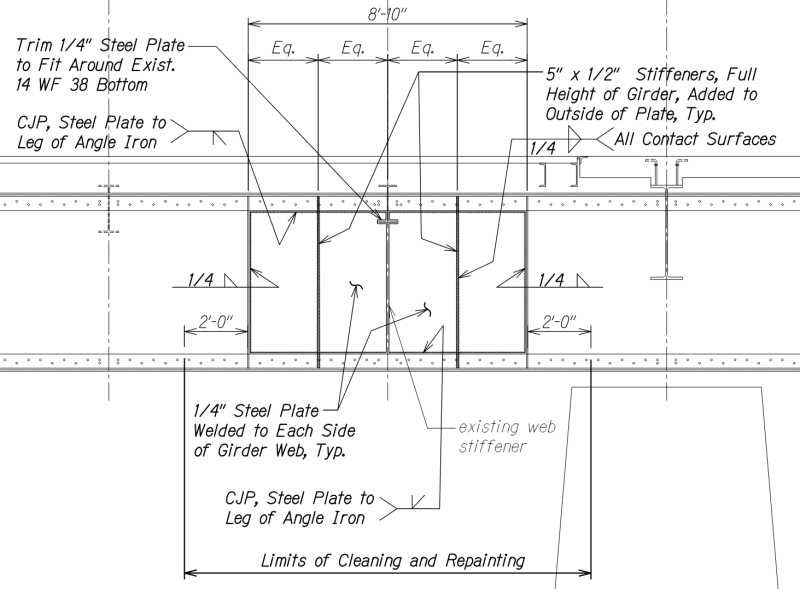