peteng_2020
Petroleum
- Mar 2, 2020
- 3
Hello,
I am trying to determine the conditions of steam flow at the inlet to my steam coil. I have marked up a drawing found online and listed my known and unknown variables to help describe the system I am working with. I began working through the problem this morning, and came to the conclusion that I need one of the following variables to determine the others: the differential pressure, the flow rate through my pipe, or the velocity of the steam. I began calculating the pressure drop throughout the system (ie. for the 10 elbows and the 4 gate valves) but got hung up on calculating the pressure drop for the length of sch. 80 pipe (98 ft.) since I needed to calculate the reynolds number and did not have the flow rate to do so. How can I figure out these variables so I am able to input the flow rate into my steam coil calculation? Or is there a completely different way to break down the problem?
Any help is greatly appreciated!
I am trying to determine the conditions of steam flow at the inlet to my steam coil. I have marked up a drawing found online and listed my known and unknown variables to help describe the system I am working with. I began working through the problem this morning, and came to the conclusion that I need one of the following variables to determine the others: the differential pressure, the flow rate through my pipe, or the velocity of the steam. I began calculating the pressure drop throughout the system (ie. for the 10 elbows and the 4 gate valves) but got hung up on calculating the pressure drop for the length of sch. 80 pipe (98 ft.) since I needed to calculate the reynolds number and did not have the flow rate to do so. How can I figure out these variables so I am able to input the flow rate into my steam coil calculation? Or is there a completely different way to break down the problem?
Any help is greatly appreciated!
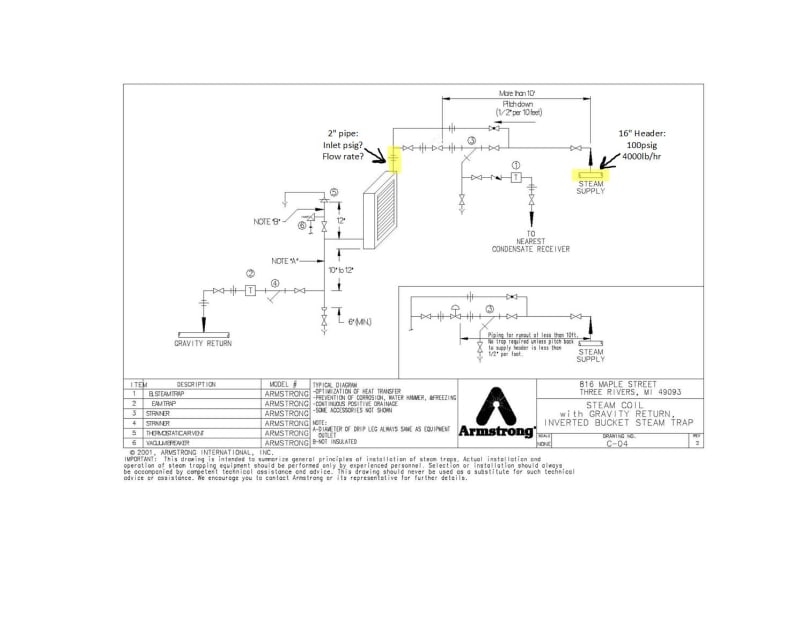