Pavan Kumar
Chemical
Hi All,
I need some guidance on the need for sizing the Pressure Control valve on the Steam Mains. The Steam Mains is served by two identical boilers each rated for 47000 kg/hr steam capacity at 12 bar(g). The steams mains supplies steam to users at 11 bar(g). It has been proposed to install a Pressure Control Valve on the Steam Mains that will be set at 14 bar(g). The purpose is to vent excess steam to atmosphere when the user load falls to prevent the header pressure from rising above 14 bar(g). The total capacity of the two boilers is 2*47000=94000 kg/hr. My question is that the Pressure Control Valve should be sized for the full load of 94000 kg/hr with 14 bar(g) upstream and 0.5 bar(g) downstream?. The 0.5 bar is the assumed pressure drop in the silencer (muffler) that is downstream of the Control valve before it vents to atmosphere. Or should I take credit of the Boiler PSVs capacities there by and reduce the size of the Control valve. I wanted to know what the sizing basis is normally.
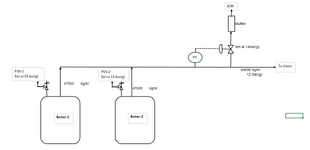
Thanks and Regards,
Pavan Kumar
I need some guidance on the need for sizing the Pressure Control valve on the Steam Mains. The Steam Mains is served by two identical boilers each rated for 47000 kg/hr steam capacity at 12 bar(g). The steams mains supplies steam to users at 11 bar(g). It has been proposed to install a Pressure Control Valve on the Steam Mains that will be set at 14 bar(g). The purpose is to vent excess steam to atmosphere when the user load falls to prevent the header pressure from rising above 14 bar(g). The total capacity of the two boilers is 2*47000=94000 kg/hr. My question is that the Pressure Control Valve should be sized for the full load of 94000 kg/hr with 14 bar(g) upstream and 0.5 bar(g) downstream?. The 0.5 bar is the assumed pressure drop in the silencer (muffler) that is downstream of the Control valve before it vents to atmosphere. Or should I take credit of the Boiler PSVs capacities there by and reduce the size of the Control valve. I wanted to know what the sizing basis is normally.
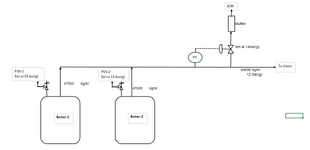
Thanks and Regards,
Pavan Kumar