Hi, I'm working on a large extruder.
It's a 150HP twin screw job with about twenty modules. Each module is electrically heated with 2 to 4kW of electrical heater. The drive is also adding 150HP of shearing heat.
Each module has a PID running its temperature control. The PID runs the module's electrical heat AND a bang-bang water valve for cooling. It's all mind-bendingly dynamic as the modules get heated up to get things going then the extrusion process starts and now that dumps lots of heat so the electrical heat throttles way back. Meanwhile the water valves cycle to keep the module temps from going too high.
The issue at hand is that the module temps hover around 320°F. The cooling water is 80 to 110°F. When the extruder gets going
the noise coming out of all the modules is horrendous! It's something relating to the cooling water probably turning to steam then back to liquid.
The entire operation would be almost dead silent except for the screeching, popping, and hissing that occurs whenever a water valve is open and most are frequently open! You have to shout to be heard anywhere near the machine.
What is this exactly?
Any suggestions on how to mitigate this?
Top pipe is the cold manifold and the bottom is the return. Could those be backwards?
Keith Cress
kcress -
It's a 150HP twin screw job with about twenty modules. Each module is electrically heated with 2 to 4kW of electrical heater. The drive is also adding 150HP of shearing heat.
Each module has a PID running its temperature control. The PID runs the module's electrical heat AND a bang-bang water valve for cooling. It's all mind-bendingly dynamic as the modules get heated up to get things going then the extrusion process starts and now that dumps lots of heat so the electrical heat throttles way back. Meanwhile the water valves cycle to keep the module temps from going too high.
The issue at hand is that the module temps hover around 320°F. The cooling water is 80 to 110°F. When the extruder gets going
the noise coming out of all the modules is horrendous! It's something relating to the cooling water probably turning to steam then back to liquid.
The entire operation would be almost dead silent except for the screeching, popping, and hissing that occurs whenever a water valve is open and most are frequently open! You have to shout to be heard anywhere near the machine.
What is this exactly?
Any suggestions on how to mitigate this?
Top pipe is the cold manifold and the bottom is the return. Could those be backwards?
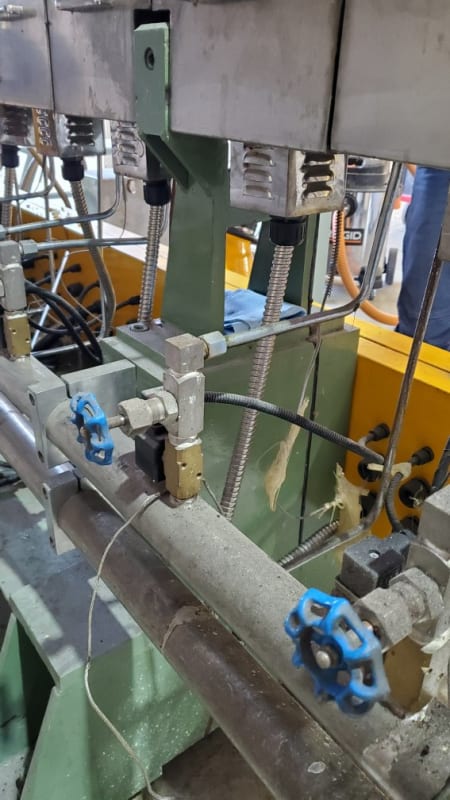
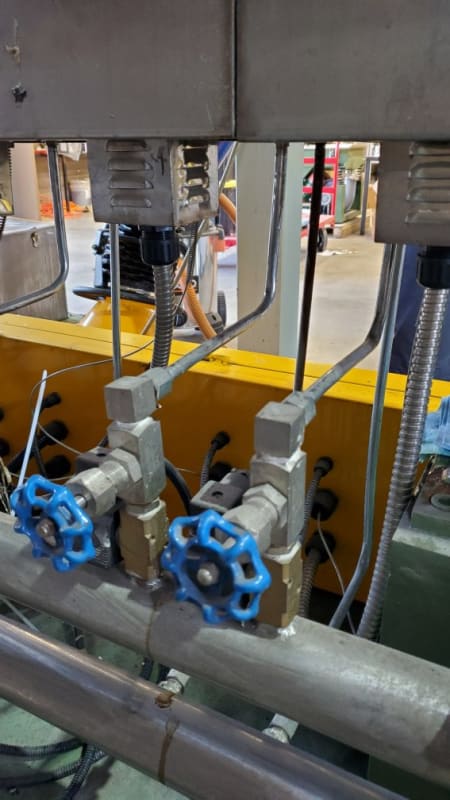
Keith Cress
kcress -