Hi All,
I am currently working on a steelwork strengthening project where the aim is to install repair plates to the existing steel beams at a cable shaft.
This is a historic structure and over time, the steel beams have severely corroded causing section losses to the flanges and the web of the beams.
The client proposed a conceptual design where they require installation of new plates to strengthen the steel beams. One of the proposals is to install a channel (PFC) section to the web of the existing I-section at either end, and connect with M12 bolts at the web only.
I am trying to come up with a design for this and trying to carry out some calculations to check the bolts. I have attached the detailed images below for reference.
My question is regarding the requirement for bolts at the top flange. Although the bolts are provided on the web, no bolts have been proposed for the top or bottom flanges. Please find some of my questions that I am looking for answers below:
- If we are doing this repair at the mid-span where we have the maximum moment, are the bolts at the web will be sufficient? Or we
- How can we know whether the design forces will be transferred to the beam using the bolts at the web only?
- How do we know whether you require bolts at the top or bottom flanges and whether there is a calculation that can be done to check whether only web bolts are sufficient to transfer the forces?
- Is this related to Shear Flow calculation?
It would be great if someone can help me on this. I have attached some details below for illustration.
I am currently working on a steelwork strengthening project where the aim is to install repair plates to the existing steel beams at a cable shaft.
This is a historic structure and over time, the steel beams have severely corroded causing section losses to the flanges and the web of the beams.
The client proposed a conceptual design where they require installation of new plates to strengthen the steel beams. One of the proposals is to install a channel (PFC) section to the web of the existing I-section at either end, and connect with M12 bolts at the web only.
I am trying to come up with a design for this and trying to carry out some calculations to check the bolts. I have attached the detailed images below for reference.
My question is regarding the requirement for bolts at the top flange. Although the bolts are provided on the web, no bolts have been proposed for the top or bottom flanges. Please find some of my questions that I am looking for answers below:
- If we are doing this repair at the mid-span where we have the maximum moment, are the bolts at the web will be sufficient? Or we
- How can we know whether the design forces will be transferred to the beam using the bolts at the web only?
- How do we know whether you require bolts at the top or bottom flanges and whether there is a calculation that can be done to check whether only web bolts are sufficient to transfer the forces?
- Is this related to Shear Flow calculation?
It would be great if someone can help me on this. I have attached some details below for illustration.
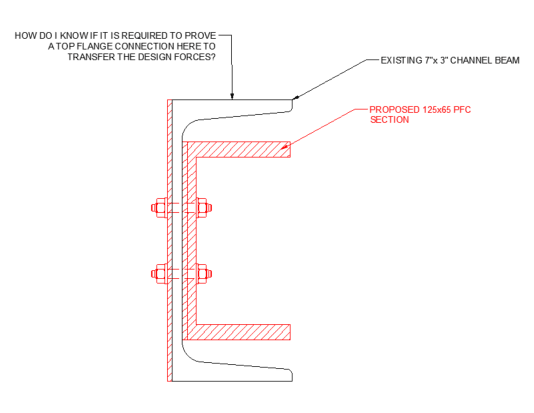
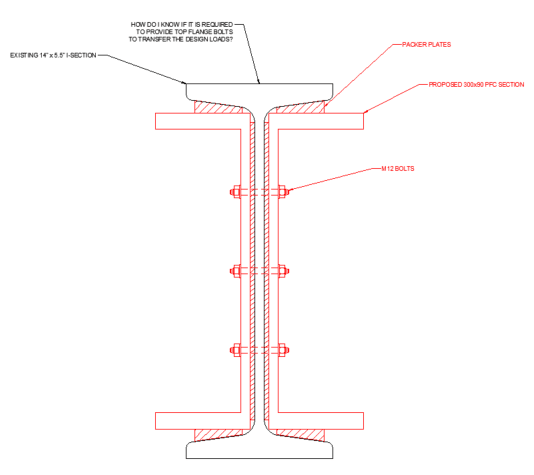
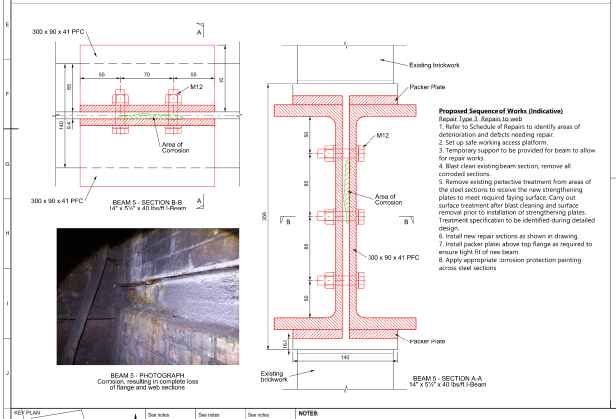