neukcm
Structural
- May 3, 2015
- 63
Good day Everyone!
In Eurocode steel design code, is there any provision regarding the design of single member composed of different steel grades? I'm talking about a box section wherein top plate is grade S275 while that of side plate is grade S355 (see attached image).
Thanks in advance
https://res.cloudinary.com/engineering-com/image/upload/v1445561739/tips/DIIFERENT_GRADE_001_jlgw2f.jpg]
In Eurocode steel design code, is there any provision regarding the design of single member composed of different steel grades? I'm talking about a box section wherein top plate is grade S275 while that of side plate is grade S355 (see attached image).
Thanks in advance
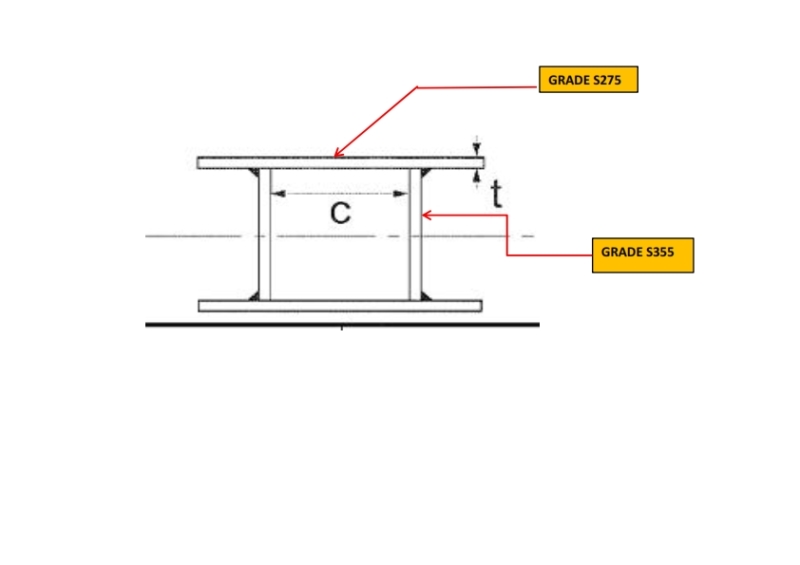