mats12
Geotechnical
- Dec 17, 2016
- 181
Im dealing with a new steel canopy (above entrance of an existing building.) I want to talk about possible issues regarding this design.
Primary steel beam is H section (8 m in span).
Secundary beams are hollow/box profiles that are connected in the middle of primary beam (it has to be in the middle).
Since cantilever is 1,40 m long I suspect that there will be quite a torsion acting on a primary H beam, but this is solved by anchoring in existing structure on the other side of secondary beams (support reaction at the end shows upward). Is that correct?
Since its a cantilever, a connection of box profile to H profile should be fixed (moment) connection. Bolts will be in tension. Im wondering what road should I choose/you suggest:
Connection 1 or connection 2.
Im worried about 1 since cantilever is connected directly to the web of H section (but there is no need for additional plates that way).
tnx for help
Primary steel beam is H section (8 m in span).
Secundary beams are hollow/box profiles that are connected in the middle of primary beam (it has to be in the middle).
Since cantilever is 1,40 m long I suspect that there will be quite a torsion acting on a primary H beam, but this is solved by anchoring in existing structure on the other side of secondary beams (support reaction at the end shows upward). Is that correct?
Since its a cantilever, a connection of box profile to H profile should be fixed (moment) connection. Bolts will be in tension. Im wondering what road should I choose/you suggest:
Connection 1 or connection 2.
Im worried about 1 since cantilever is connected directly to the web of H section (but there is no need for additional plates that way).
tnx for help
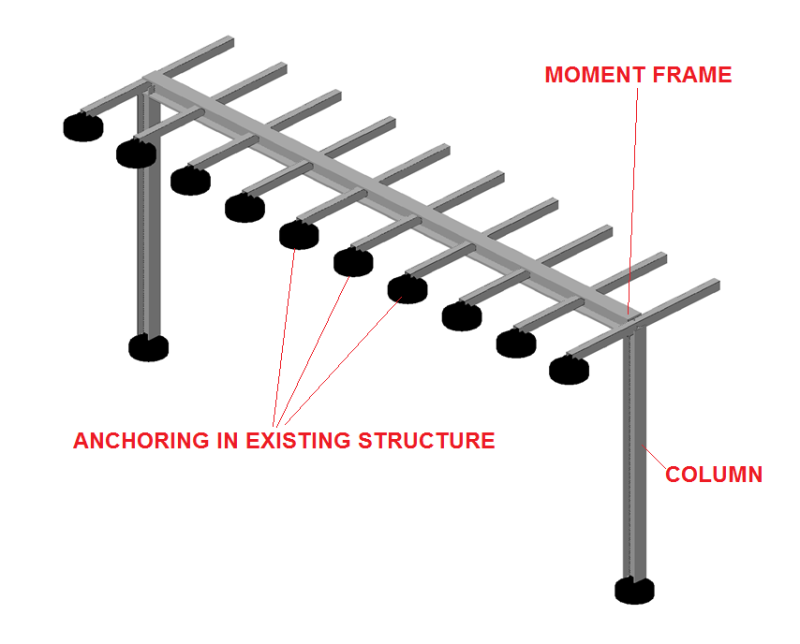
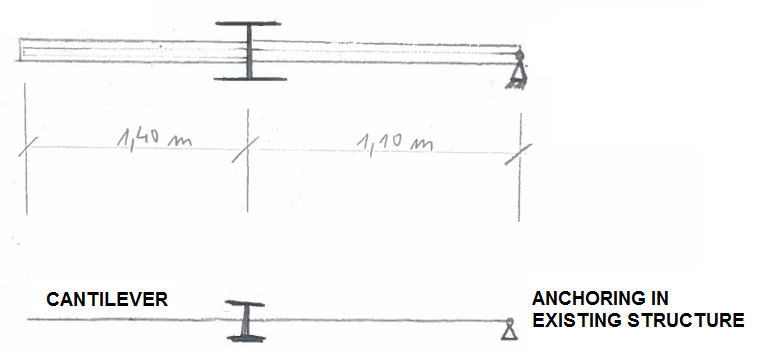
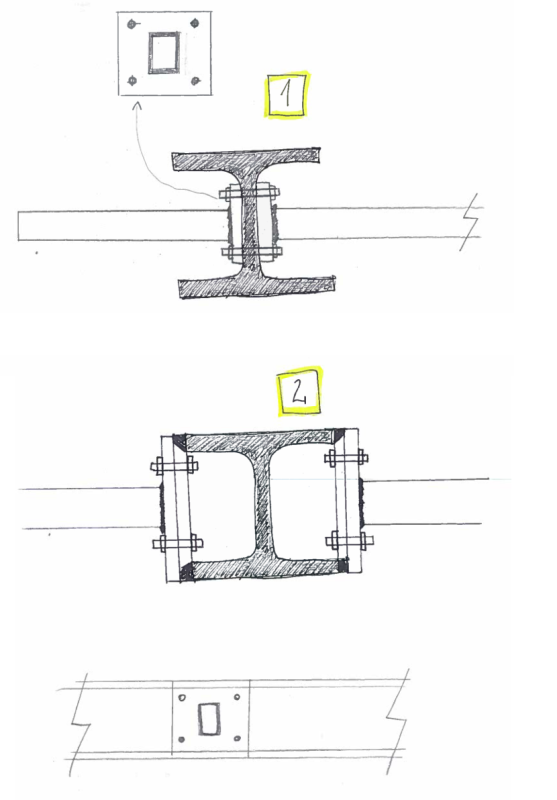