dik
Structural
- Apr 13, 2001
- 26,010
I have an unusual canopy connection with W12x30 beams framing into an HSS 8x8x0.375 column. They connect at different levels. There is a continuation of the beam on the opposite side of the column. I'm planning to field weld 5/8" end plates on the beam ends to the face of the columns as shown. Does anyone have any concerns about this approach? Worked a better approach. Thanks...
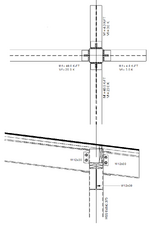
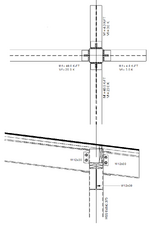
Attachments
Last edited: