I'm getting pushed pretty hard to use the detail below. The reason is pretty straight forward: compared to a column welded to a cast in plate, plumbing and erection is much easier with this detail. It definitely can be done with the welded detail however.
The photo at the bottom was taken from a related thread on this forum and shows a steel column that is supported directly above a concrete column below. While a consensus has not been reached there, my opinion is that a similar, recessed pocket detail is to blame for the cracking shown.
There are other details that I could use here but that's not what I'm seeking. What I'd like to get feedback on is a method for evaluating whether or not the detail shown below works. What needs to be checked here in order to give this a passing grade?
My specific concerns and opinions are as follows:
1) The recess forces one to either drop the top reinforcing mat or push the bars out to the side of the pocket.
2) With the mat dropped, punching shear is a beast and significant cracking can be expected as shown in the photo.
3) With the top steel moved to the side of the recess, it's tough to meet the code rules on the amount of steel that may be placed over and near the column.
4) With the top steel moved to the side of the recess, I again wonder about punching shear capacity. See the hypothetical cracks in my sketch below. My concern is exacerbated by the interrelated nature of punching shear and flexural capacity (Link) at column/slab joints. If I shift my moment capacity away from the column, does that mess with my punching shear capacity?
5) I have renovated buildings from the 70's and 80's that had similar details but with drop panels. They seemed to be performing well.
I like to debate structural engineering theory -- a lot. If I challenge you on something, know that I'm doing so because I respect your opinion enough to either change it or adopt it.
The photo at the bottom was taken from a related thread on this forum and shows a steel column that is supported directly above a concrete column below. While a consensus has not been reached there, my opinion is that a similar, recessed pocket detail is to blame for the cracking shown.
There are other details that I could use here but that's not what I'm seeking. What I'd like to get feedback on is a method for evaluating whether or not the detail shown below works. What needs to be checked here in order to give this a passing grade?
My specific concerns and opinions are as follows:
1) The recess forces one to either drop the top reinforcing mat or push the bars out to the side of the pocket.
2) With the mat dropped, punching shear is a beast and significant cracking can be expected as shown in the photo.
3) With the top steel moved to the side of the recess, it's tough to meet the code rules on the amount of steel that may be placed over and near the column.
4) With the top steel moved to the side of the recess, I again wonder about punching shear capacity. See the hypothetical cracks in my sketch below. My concern is exacerbated by the interrelated nature of punching shear and flexural capacity (Link) at column/slab joints. If I shift my moment capacity away from the column, does that mess with my punching shear capacity?
5) I have renovated buildings from the 70's and 80's that had similar details but with drop panels. They seemed to be performing well.
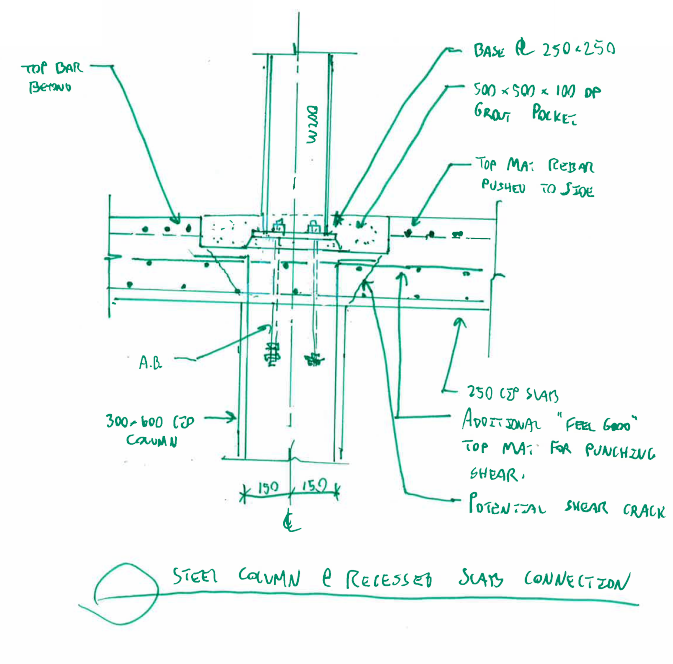
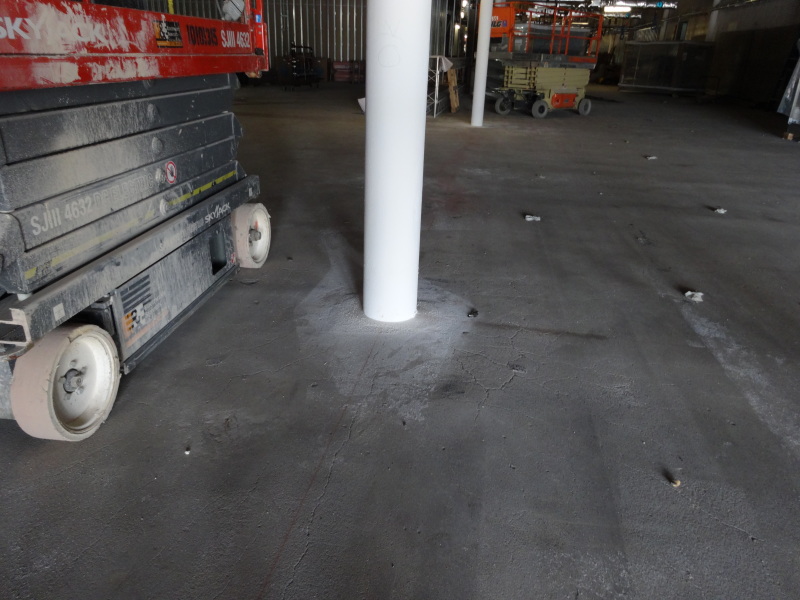
I like to debate structural engineering theory -- a lot. If I challenge you on something, know that I'm doing so because I respect your opinion enough to either change it or adopt it.