engineering3DTEK
Structural
Hello fellow engineers,
AISC design guide 34
I am designing base connection for a guardrail system. I apply 0.250 kips force on the top rail factored with 1.6 (LRFD), therefore 0.4 kips shear force on top rail. The height of my guardrail system is 42". So I get a moment of 0.4 X42 = 16.8 kip-in momnent at the base connection. But for this force, I am unable to design expansion or chemical anchor base connection. The connection fails. The depth of available concrete slab is just 3" (4000 psi).
Please refer to the attachment (PDF) & image depecting the exact scenario.
Could someone please suggest me how to distribute the forces to anchor bolts & how could I make this connection work.
Thanks you.
AISC design guide 34
I am designing base connection for a guardrail system. I apply 0.250 kips force on the top rail factored with 1.6 (LRFD), therefore 0.4 kips shear force on top rail. The height of my guardrail system is 42". So I get a moment of 0.4 X42 = 16.8 kip-in momnent at the base connection. But for this force, I am unable to design expansion or chemical anchor base connection. The connection fails. The depth of available concrete slab is just 3" (4000 psi).
Please refer to the attachment (PDF) & image depecting the exact scenario.
Could someone please suggest me how to distribute the forces to anchor bolts & how could I make this connection work.
Thanks you.
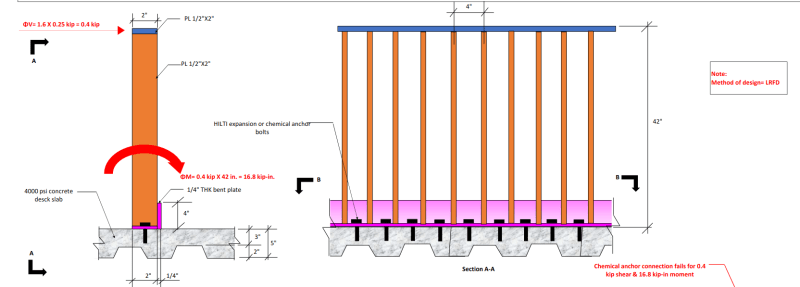