-
1
- #1
Ewi2010
Structural
- Nov 6, 2018
- 3
Hi Guys,
I am new here and a young structural engineer. I am busy checking steel connection on rooftop Telecom structures and I am firstly not sure how there connections would be modeled and then which hand calculations would need to be done ( I am Using Spacegass). Will it be assume that these Ubolt connections are moment connections or not? I was thinking of calculating some sort of yield lines and determining the moment capacity of the plates due to the tension forces in the bolts. Any advice would be appreciated!
If anyone is willing to help I upload a sample of the type of calc I am doing at the moment.
Thanks in advance!
I am new here and a young structural engineer. I am busy checking steel connection on rooftop Telecom structures and I am firstly not sure how there connections would be modeled and then which hand calculations would need to be done ( I am Using Spacegass). Will it be assume that these Ubolt connections are moment connections or not? I was thinking of calculating some sort of yield lines and determining the moment capacity of the plates due to the tension forces in the bolts. Any advice would be appreciated!
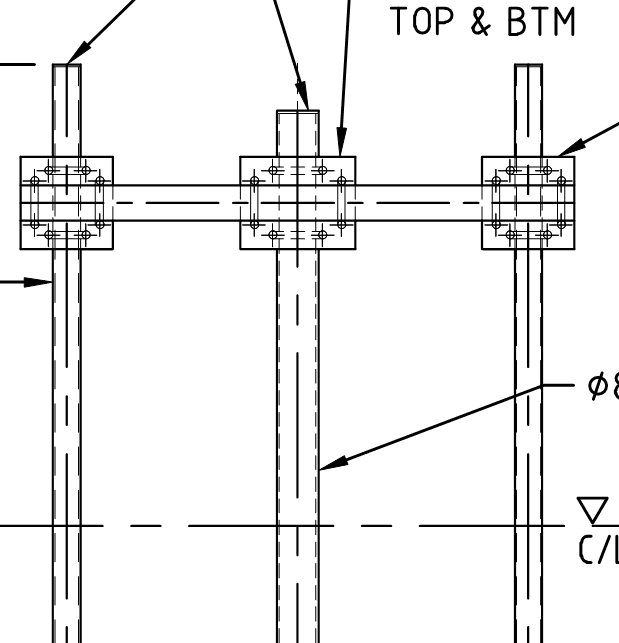

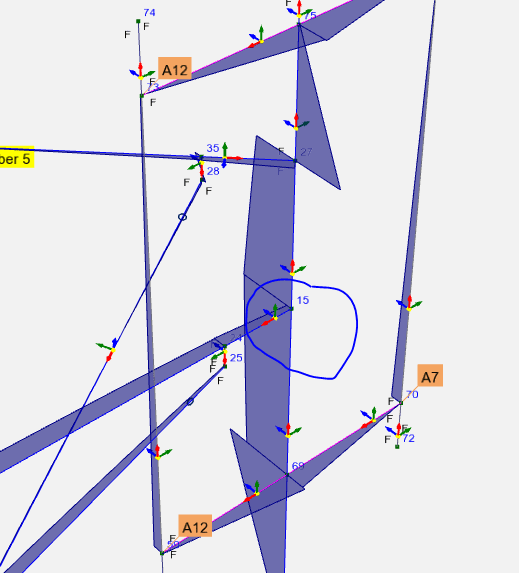
If anyone is willing to help I upload a sample of the type of calc I am doing at the moment.
Thanks in advance!