lolobau
Civil/Environmental
- Dec 10, 2012
- 115
Hi
I was wondering why do we always cut the angle sections by truss connections straight?
When we would cut it parallel to the main bottom and top members then we could reduce the gusset plate size by a significant amount.
This would also lead to shorter "gaps" between the members fixing points which should be also better for the load transfer, or?
Am I overseeing something?
By wooden trusses this is usually done this way, so why not by steel?
See attached images
I was wondering why do we always cut the angle sections by truss connections straight?
When we would cut it parallel to the main bottom and top members then we could reduce the gusset plate size by a significant amount.
This would also lead to shorter "gaps" between the members fixing points which should be also better for the load transfer, or?
Am I overseeing something?
By wooden trusses this is usually done this way, so why not by steel?
See attached images
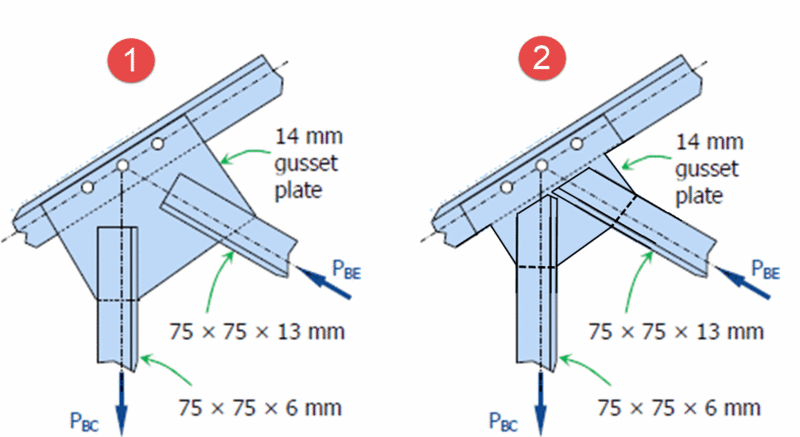
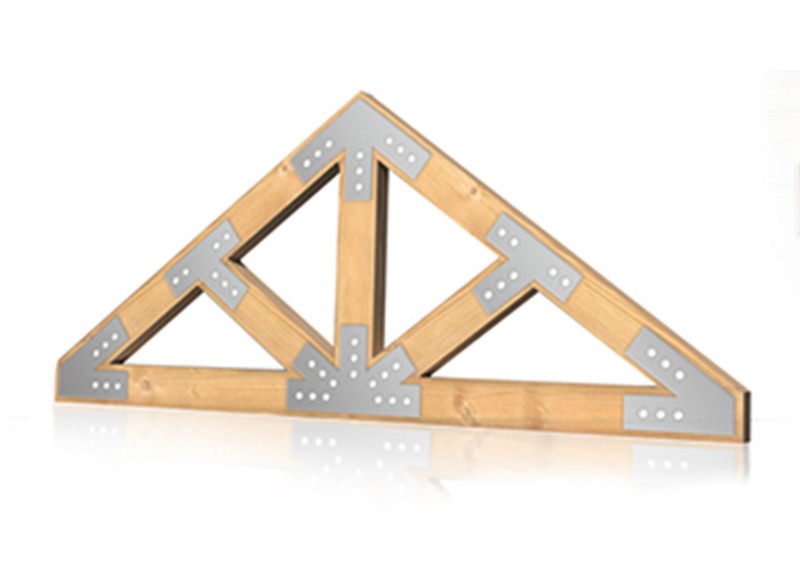
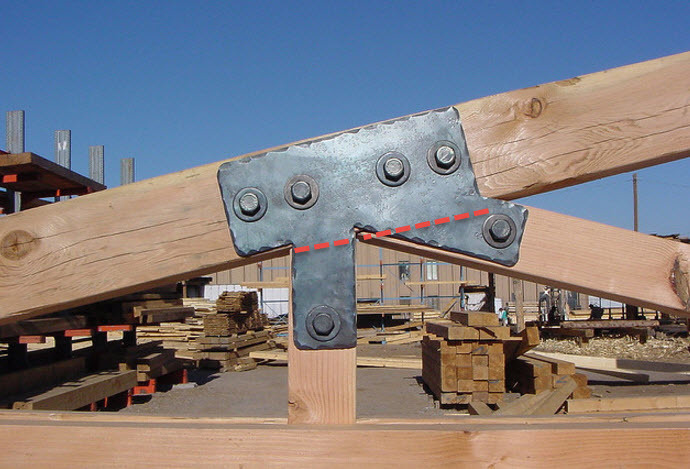
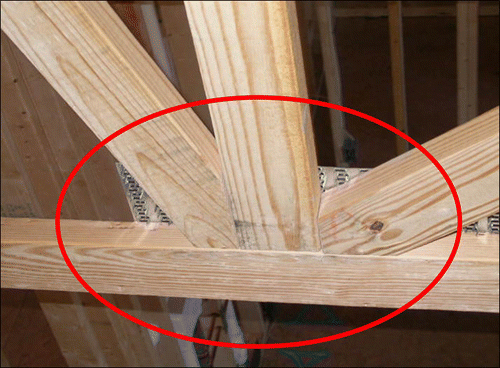
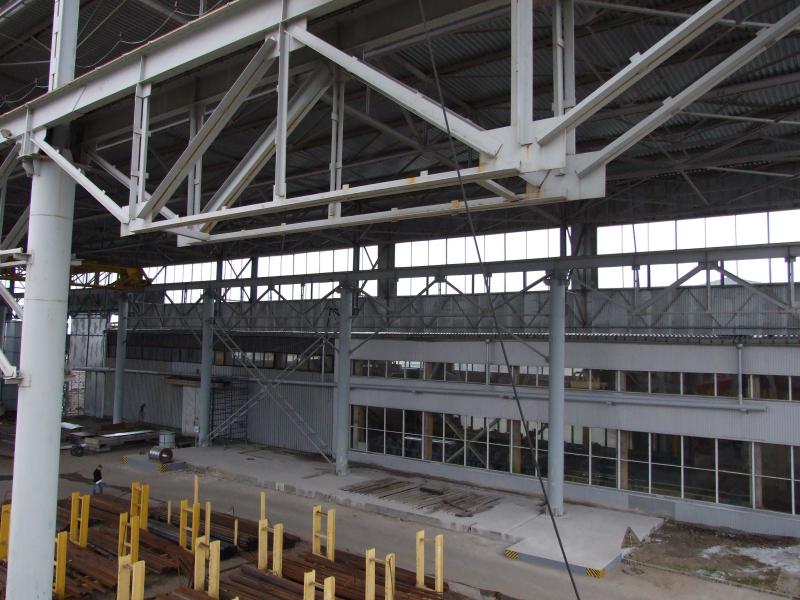