Good Morning,
I'm designing a steel transfer structure, where a number of the transferring columns are skewed relative to the supporting transfer beam. Thinking about this, I would like to include a stiff plate below the transferring column, and then include stiffeners extending the full width of the plate. I've attached a sketch of what I am thinking to do here. If anyone have any thoughts about this approach or any input / resources that might relate to this condition, it would be greatly appreciated.
Thanks so much!
I'm designing a steel transfer structure, where a number of the transferring columns are skewed relative to the supporting transfer beam. Thinking about this, I would like to include a stiff plate below the transferring column, and then include stiffeners extending the full width of the plate. I've attached a sketch of what I am thinking to do here. If anyone have any thoughts about this approach or any input / resources that might relate to this condition, it would be greatly appreciated.
Thanks so much!
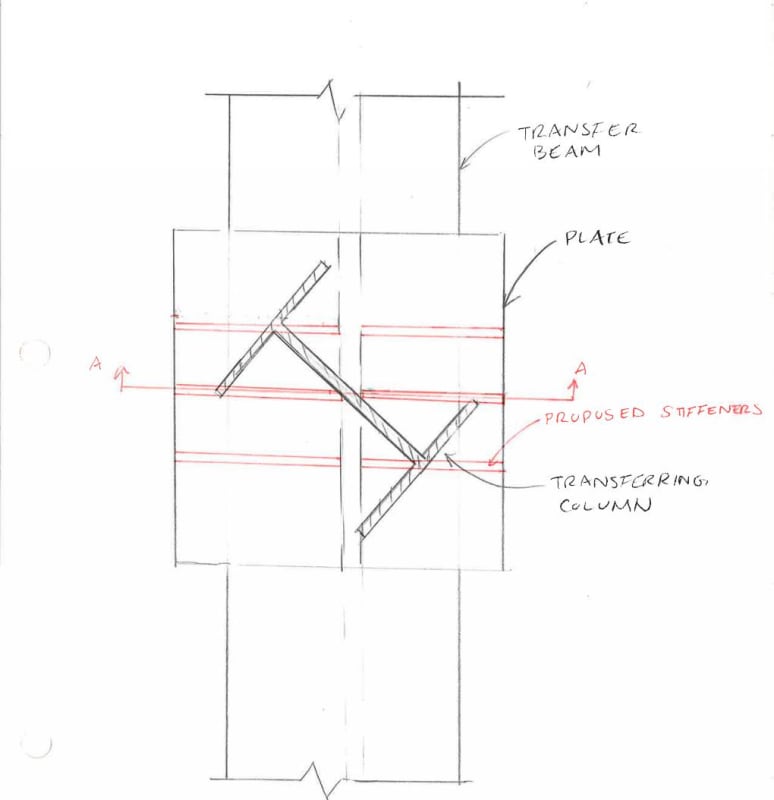
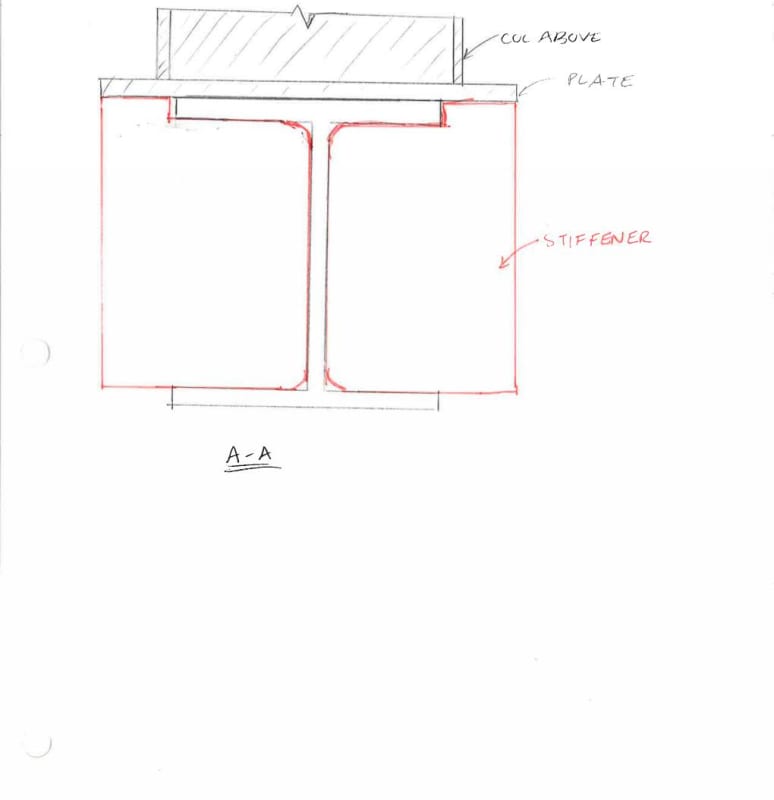