Hi,
I am having some difficultly with a strain gauge measurement and I am looking for some insight.
In a torque application, I see a drift with my strain gauges (2 half bridges on opposing sides of the shaft). I am calibrating them using 2 known points to create a calibration line. It appears that over time the 0 point of that calibration curve will shift, but then also return to 0 after about 24 hours. See actual measurements below. This graph shows ~15,000 measurements taken over ~48 hours where it was calibrated at the beginning. I am not sure why there is a drift and then a drift back.
Setup information:
Shaft:
0.5” diameter 4140 shaft heat treated to 53HRC
Environment:
Elevated temperature environment: ~ 135 F
Adhesive:
Pemabond 820 High temperature Cyanoacrylate
Stain gauge:
Steel compensated.
2x Half-bridge Strain Gauge
1 kΩ per quarter-bridge
3 mm active length
Excitation voltage: 5VDC with dc meter
I am having some difficultly with a strain gauge measurement and I am looking for some insight.
In a torque application, I see a drift with my strain gauges (2 half bridges on opposing sides of the shaft). I am calibrating them using 2 known points to create a calibration line. It appears that over time the 0 point of that calibration curve will shift, but then also return to 0 after about 24 hours. See actual measurements below. This graph shows ~15,000 measurements taken over ~48 hours where it was calibrated at the beginning. I am not sure why there is a drift and then a drift back.
Setup information:
Shaft:
0.5” diameter 4140 shaft heat treated to 53HRC
Environment:
Elevated temperature environment: ~ 135 F
Adhesive:
Pemabond 820 High temperature Cyanoacrylate
Stain gauge:
Steel compensated.
2x Half-bridge Strain Gauge
1 kΩ per quarter-bridge
3 mm active length
Excitation voltage: 5VDC with dc meter
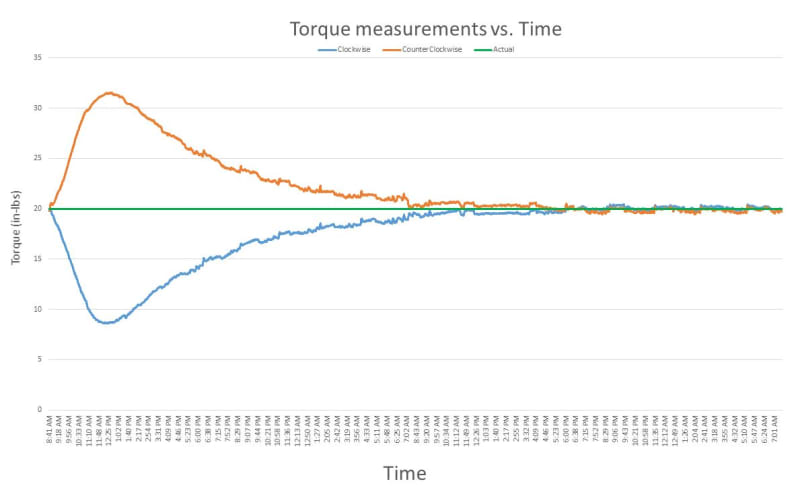