mats12
Geotechnical
- Dec 17, 2016
- 181
I need to strenghten a bottom flange of a steel profile (IPE 270).
Flange is 135 mm wide and 10 mm thick, my steel plate has to be 15 mm thick and 120 mm wide. I cant use wider steel plate.
I want to connect a steel plate to bottom flange with fillet welds on bot sides as shown in attached image.
Thats not really my cup of tea so Im wondering is it OK that steel plate is that thick - fillet weld is not made to the bottom of a steel plate but only to about 1/3 of its thickness. Is that OK?
I have to calculate a shear flow between a steel profile and a steel plate and consider this while designing a weld. Right? Any other forces acting on a weld?
Sorry for bad English.
TNX
Flange is 135 mm wide and 10 mm thick, my steel plate has to be 15 mm thick and 120 mm wide. I cant use wider steel plate.
I want to connect a steel plate to bottom flange with fillet welds on bot sides as shown in attached image.
Thats not really my cup of tea so Im wondering is it OK that steel plate is that thick - fillet weld is not made to the bottom of a steel plate but only to about 1/3 of its thickness. Is that OK?
I have to calculate a shear flow between a steel profile and a steel plate and consider this while designing a weld. Right? Any other forces acting on a weld?
Sorry for bad English.
TNX
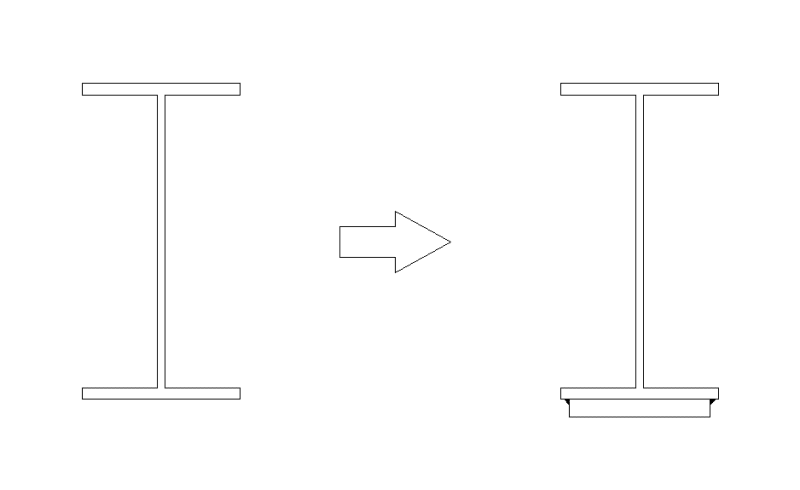
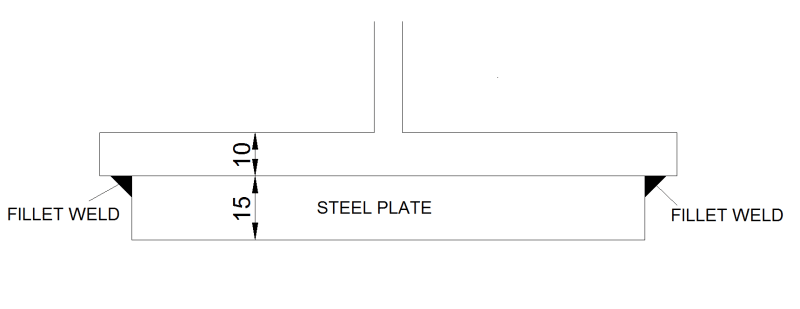