harrytos23
Student
- Nov 6, 2024
- 15
Hi, this is a structure that we designed to decrease the force as the absorber breaks (thin plates that is designed to break upon impact).
My question now is, is there a way to calculate the force after the first contact with the first plate? because I know the 1st plate will be destroyed and as well as the second but wondering how much less the impact force would be on the 2nd plate and for the rectangular tube as well. Is there any resource/book/formula that can show how forces are distributed after breakage of the material? Thank you.
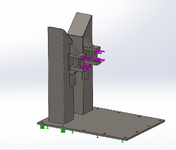
My question now is, is there a way to calculate the force after the first contact with the first plate? because I know the 1st plate will be destroyed and as well as the second but wondering how much less the impact force would be on the 2nd plate and for the rectangular tube as well. Is there any resource/book/formula that can show how forces are distributed after breakage of the material? Thank you.
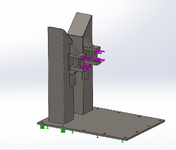