r.borghino
Structural
- Nov 25, 2024
- 11
Hi,
I am working on a problem where I have a roughly "T" shape profile (inverted) where I am applying two equal point loads to the top of the single leg. I am trying to evaluate stresses on the flat plate caused by the cantilever leg. I usually simplify this problem and simply assume a flat plate with a moment applied at midspan. However, I'd like to make a more "real" analysis without going into FEM. I've looked through Roark and other sources but to no avail. I am definitely missing something... do you have any help or insights to spare? (is it even worth the effort?) Thanks!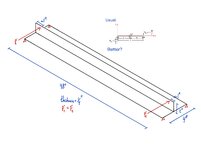
I am working on a problem where I have a roughly "T" shape profile (inverted) where I am applying two equal point loads to the top of the single leg. I am trying to evaluate stresses on the flat plate caused by the cantilever leg. I usually simplify this problem and simply assume a flat plate with a moment applied at midspan. However, I'd like to make a more "real" analysis without going into FEM. I've looked through Roark and other sources but to no avail. I am definitely missing something... do you have any help or insights to spare? (is it even worth the effort?) Thanks!
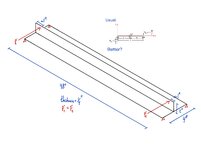