M.IDR
Structural
- Dec 31, 2020
- 43
Hello,
Cables are suspended between two steel posts and anchored as shown in the picture. How these Cable needs to be designed and What are the main components provided in the structural design drawings for construction.
3D View.
Does any one have slightest idea?
Cables are suspended between two steel posts and anchored as shown in the picture. How these Cable needs to be designed and What are the main components provided in the structural design drawings for construction.

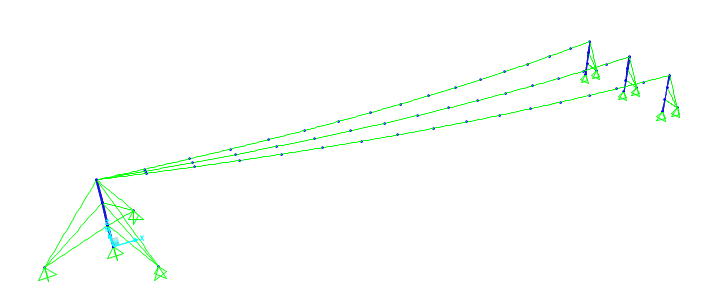