fp23
Structural
- Aug 2, 2024
- 20
I'm being asked if I can design a glass railing for a client. I'd like to learn glass design and I don't mind eating it on my fee to break into it, but this project doesn't warrant buying an expensive software like RFEM. My project would be a glass panel system with 2 circular glass clamps at each stair tread tread and a steel plate top rail. I think the steel plate top rail would provide enough stiffness to act as a support but i'd like to check it as a cantilevered system and keep the top rail as redundancy if I can. I've attached a photo of what the base connection would look like but my railing would have a continuous steel top plate with corners. Based on the research I've done, it seems like I would want to build an FEM model of a glass panel to be able to look at stress concentrations at the glass clamps.
My questions are:
1) For those of you who have done glass design like this, do you agree that an FEM model would be required to accurately check for stress concentrations at the glass clamps? If the glass was simply spanning between the top rail and the tread do you think an FEM model would still be needed to check for stress concentrations at the clamps?
2) I typically use Risa 3d but it's my understanding that Risa can't analyze brittle materials so even if I created a material with glass properties I shouldn't trust an FEM analysis for glass from Risa. Does this seem correct?
3) Any other affordable softwares or design guides out there for something like this? The most affordable option I've found so far is a 1-month license for RFEM at $600.
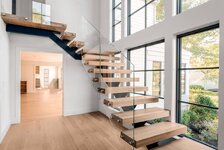
My questions are:
1) For those of you who have done glass design like this, do you agree that an FEM model would be required to accurately check for stress concentrations at the glass clamps? If the glass was simply spanning between the top rail and the tread do you think an FEM model would still be needed to check for stress concentrations at the clamps?
2) I typically use Risa 3d but it's my understanding that Risa can't analyze brittle materials so even if I created a material with glass properties I shouldn't trust an FEM analysis for glass from Risa. Does this seem correct?
3) Any other affordable softwares or design guides out there for something like this? The most affordable option I've found so far is a 1-month license for RFEM at $600.
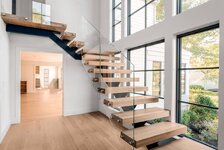