dis_
Structural
- Nov 19, 2020
- 17
I have this offset column as shown below. The transfer point load from the column above is 1000kN.
I am at a point where I can design it using strut & tie or a normal beam as per AS3600 since strut angle is about 30 degree.
When I design it as strut tie, I find the strut strength fails while it passes easily with ligs if it is designed as a normally beam. The reason why STM fails is strut strength has been reduced a lot by efficiency factor beta_s and it doesn't consider the ligs contribution even if I add ligs in. The Code does allow me to consider the enhancement by the reinforcement, by which I can design the strut as column. But the reinforcement has to be parallel to the strut with ligs at a angle in this case as well, which is not practical.
My question is, if I provide normally vertical ligs, how much strength the strut will improve if I design it using STM since the strut has been confined in some way. Any thoughts?
I am at a point where I can design it using strut & tie or a normal beam as per AS3600 since strut angle is about 30 degree.
When I design it as strut tie, I find the strut strength fails while it passes easily with ligs if it is designed as a normally beam. The reason why STM fails is strut strength has been reduced a lot by efficiency factor beta_s and it doesn't consider the ligs contribution even if I add ligs in. The Code does allow me to consider the enhancement by the reinforcement, by which I can design the strut as column. But the reinforcement has to be parallel to the strut with ligs at a angle in this case as well, which is not practical.
My question is, if I provide normally vertical ligs, how much strength the strut will improve if I design it using STM since the strut has been confined in some way. Any thoughts?
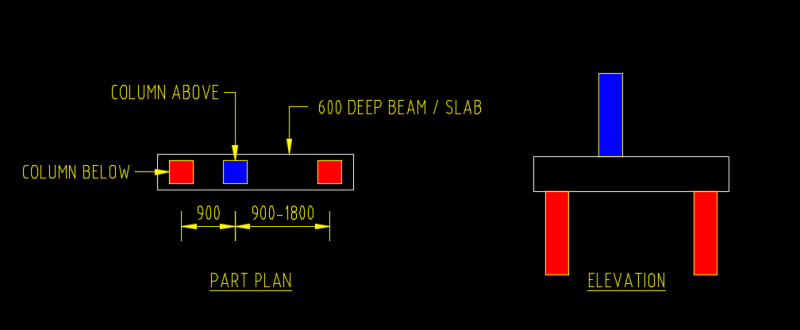