-
1
- #1
KootK
Structural
- Oct 16, 2001
- 18,561
I'm seeking guidance and/or references for dealing with substantial openings in precast double tee flanges. I'd think this to be a pretty common thing but I've not yet hit the jackpot on google. Some starter thoughts:
- strut and tie as always. 2" flanges though. Not getting a lot of bar in there.
- design the stems across the opening pretending that there's no flange at all.
- even designing the member sans flanges, I still worry about the vestigial flange bits absorbing compression and buckling etc.
As with all things that get prefabbed, shipping and handling stresses inducing cracking is proabably as important as anything else.
Recommendations?
I like to debate structural engineering theory -- a lot. If I challenge you on something, know that I'm doing so because I respect your opinion enough to either change it or adopt it.
- strut and tie as always. 2" flanges though. Not getting a lot of bar in there.
- design the stems across the opening pretending that there's no flange at all.
- even designing the member sans flanges, I still worry about the vestigial flange bits absorbing compression and buckling etc.
As with all things that get prefabbed, shipping and handling stresses inducing cracking is proabably as important as anything else.
Recommendations?
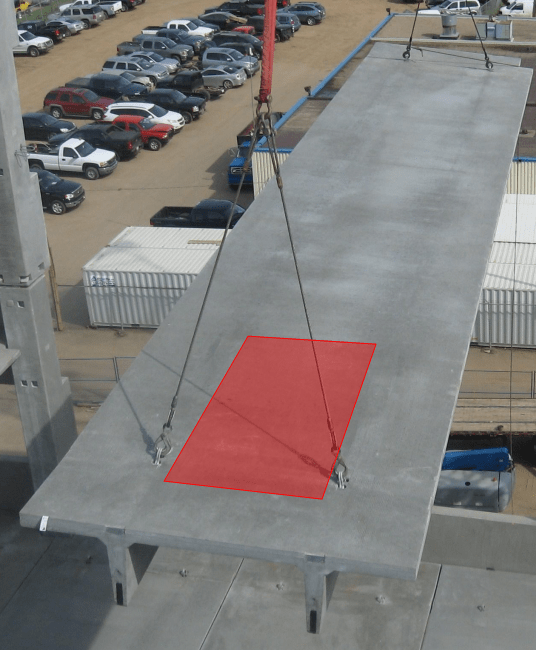
I like to debate structural engineering theory -- a lot. If I challenge you on something, know that I'm doing so because I respect your opinion enough to either change it or adopt it.