Socko525
Structural
- Nov 25, 2023
- 6
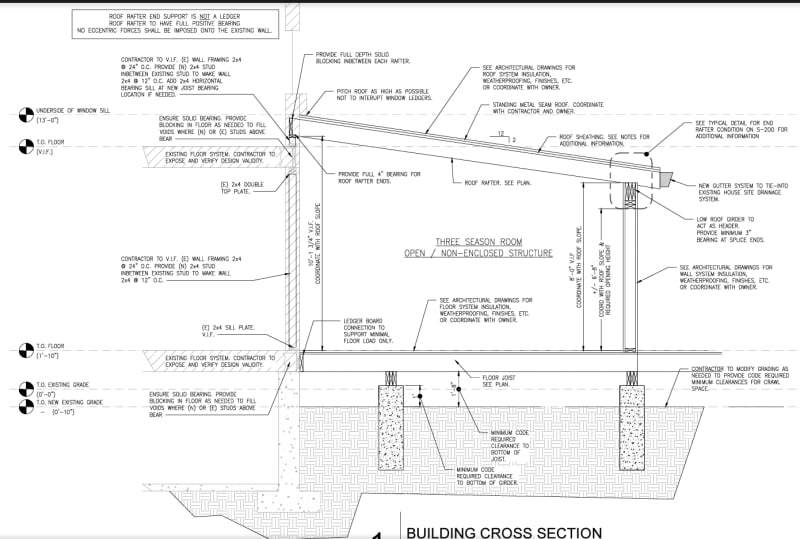
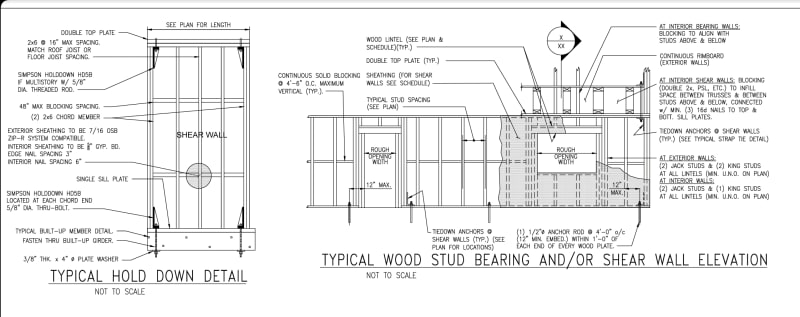
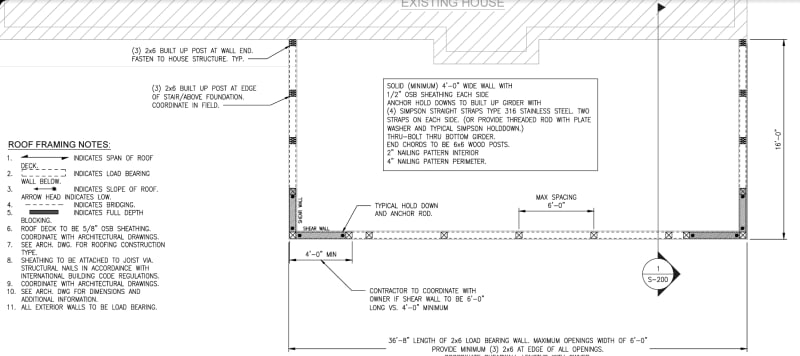
I'm in the process of building what started out as a screened porch and is seemingly shifting more towards a 3 season room. I wasn't originally worried about shear walls when it would all be screened in, but the client is looking to possibly add 4 track vertical patio windows (the vinyl memory film kind).
For a little background, the job is in Orange County, New York (so no major wind or seismic issues). The overall space is 16'x36'. The walls will be 2x6, with a 3' high knee wall around the entire perimeter. I plan to install 7/16" Zip system on the outside as well. The roof is going to be lean-to style standing seam metal.
The plans I have call for a 4'x4' shear wall at the outside corners, but the client isn't happy at how of the view would be blocked.
I've seen a lot of screened in porches converted to 3 season rooms or even sunrooms and they don't seem to go through the effort of building shear walls (though I wonder if that's because most of those conversions are smaller than this space).
So I'm trying to find a way to avoid or adjust the shear wall. I was thinking of adding diagonal lateral blocking within the knee wall for the entire perimeter. I also entertained adding 7/16" Zip system to the inside of the kneel wall as well and then covering it with wainscoting.
If I could lessen the shear wall to 2' or maybe even 3' that might work. Or perhaps add a decorative small window within the shear wall I think that would work.
I'm not sure what other information you'd need, but any thoughts, feedback or alternatives would be appreciated!