I am working on transitioning over to the built-in *Superelastic definitions of nitinol in Abaqus, and at the same time working to include plasticity (new model requires very high strains). I'm having a rough time including the Material Hardening and Material Hardening Modifications.
I built a simple unit-cell mesh and pull on it with various amounts of strain. Here's the output:
There's obviously a few things wrong here, so let's tackle them one at a time (they may actually be linked, but I'll discuss them separately):
Upper plateau stress superelastic window:
The end of my superelastic window should be around 6.5% for this material model. Note, however, when going beyond the martensitic elastic region that with each subsequent loop (12%, 14%, 16%) that the original length of the upper plateau is preserved, so I seemingly have a material which exhibits elasticity almost to 10% after a 15% pull. This is obviously nowhere near correct.
Degradation of plateau stresses with subsequent loops:
I've attempted to use the Super Elastic Hardening Modifications table provided, but the documentation is woefully inadequate (as I've found typical of Abaqus) to actually help a user correctly use the features rather than just tell what is is. I'm wondering if I were able to use this correctly then the length of the upper plateau might also fall in line?
Any thoughts?
I built a simple unit-cell mesh and pull on it with various amounts of strain. Here's the output:
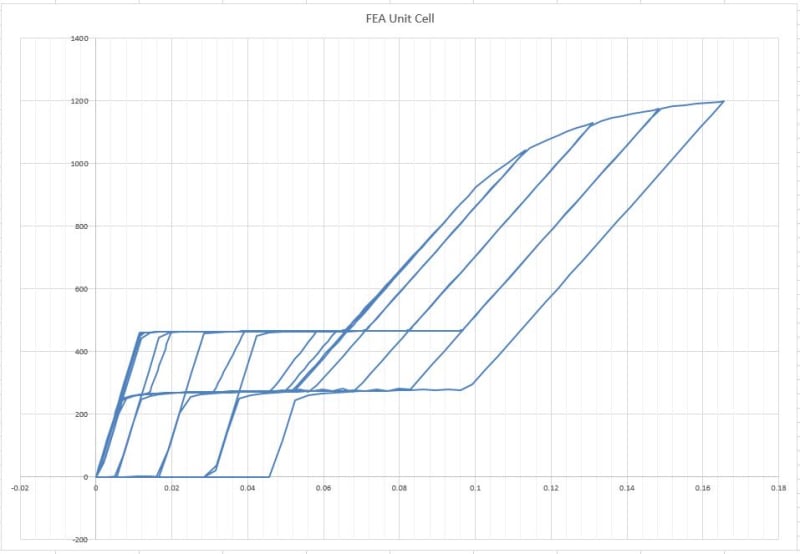
There's obviously a few things wrong here, so let's tackle them one at a time (they may actually be linked, but I'll discuss them separately):
Upper plateau stress superelastic window:
The end of my superelastic window should be around 6.5% for this material model. Note, however, when going beyond the martensitic elastic region that with each subsequent loop (12%, 14%, 16%) that the original length of the upper plateau is preserved, so I seemingly have a material which exhibits elasticity almost to 10% after a 15% pull. This is obviously nowhere near correct.
Degradation of plateau stresses with subsequent loops:
I've attempted to use the Super Elastic Hardening Modifications table provided, but the documentation is woefully inadequate (as I've found typical of Abaqus) to actually help a user correctly use the features rather than just tell what is is. I'm wondering if I were able to use this correctly then the length of the upper plateau might also fall in line?
Any thoughts?