Sachin Poudel
Mechanical
I did support lug FEA as per ASME Section VIII Div-2, Part 5, Elastic Stress Analysis Method (5.2.2). The model in analysis consists of Support Lug Assembly, Heads, Shell and fillet weld between Support Lug and Shell. The material properties of Shell and Support Lugs are as follows:
Allowable Stress: 16,025 @ 375 F
Yield Stress: 17,925 psi @ 375 F
There is high stress in Weld. How should the stress in weld be interpreted as per Div-2 part 5? What are allowable stress in welds for Elastic Stress Analysis (Div-2, 5.2.2)?
I found that the stress in shell and welds increases as the position of support lug approaches shell-head junction. Can this be due to Secondary stress playing role near the shell-head junction? If so, can we treat the bending stress in weld as secondary stress?
Allowable Stress: 16,025 @ 375 F
Yield Stress: 17,925 psi @ 375 F
There is high stress in Weld. How should the stress in weld be interpreted as per Div-2 part 5? What are allowable stress in welds for Elastic Stress Analysis (Div-2, 5.2.2)?
I found that the stress in shell and welds increases as the position of support lug approaches shell-head junction. Can this be due to Secondary stress playing role near the shell-head junction? If so, can we treat the bending stress in weld as secondary stress?
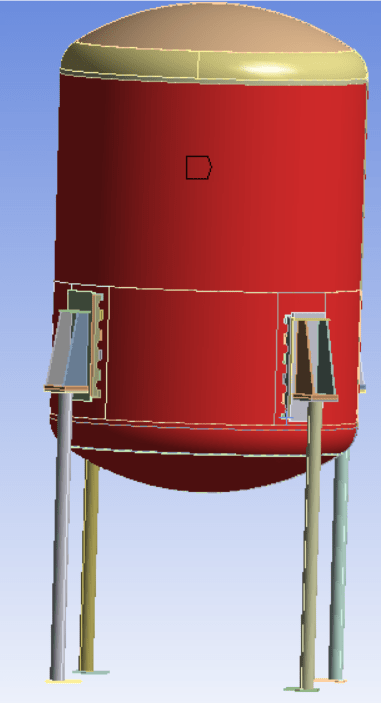
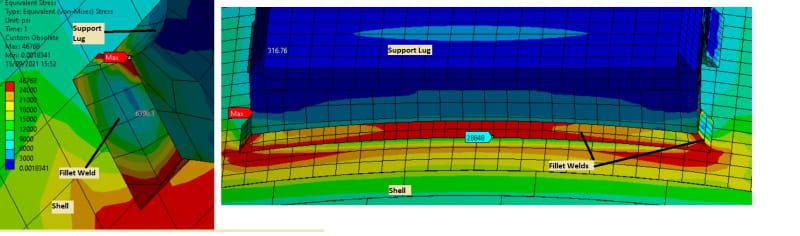