I have a rectangular steel plate with a bolt in the middle and pinned supports at each extreme.
The bolt transmits a force to one side of the plate. Theoretically (following linear statics), both supports have the same reaction force value. But is this tru in reality? Doesnt large deformations + plastic deformations change the 50/50 reaction distribution? Which support gets more load? My intuition tells me that the compressed support 1 will have a greater reaction force than the tensioned support 2. Both supports are also bolts.
I attach a quick sketch of the problem:
The bolt transmits a force to one side of the plate. Theoretically (following linear statics), both supports have the same reaction force value. But is this tru in reality? Doesnt large deformations + plastic deformations change the 50/50 reaction distribution? Which support gets more load? My intuition tells me that the compressed support 1 will have a greater reaction force than the tensioned support 2. Both supports are also bolts.
I attach a quick sketch of the problem:
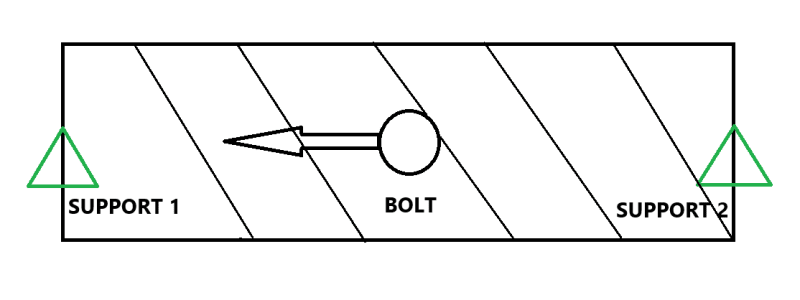