T_Bat
Structural
- Jan 9, 2017
- 213
Hey everyone,
I have a job with a brick wrapped cupola. At the case where the veneer sits on the down slope, I'm not sure how to support it. I'm thinking of ripping some blocking to so that my brick angle can sit flat (no bent plate) and I can tie it back to the cupola framing. I assume they architect can flash behind the brick, over the angle, and down the blocking. Has anyone ever run across this before?
For the other direction, I'm planning to follow the IRC provisions and weld tabs to the angle.
I have a job with a brick wrapped cupola. At the case where the veneer sits on the down slope, I'm not sure how to support it. I'm thinking of ripping some blocking to so that my brick angle can sit flat (no bent plate) and I can tie it back to the cupola framing. I assume they architect can flash behind the brick, over the angle, and down the blocking. Has anyone ever run across this before?
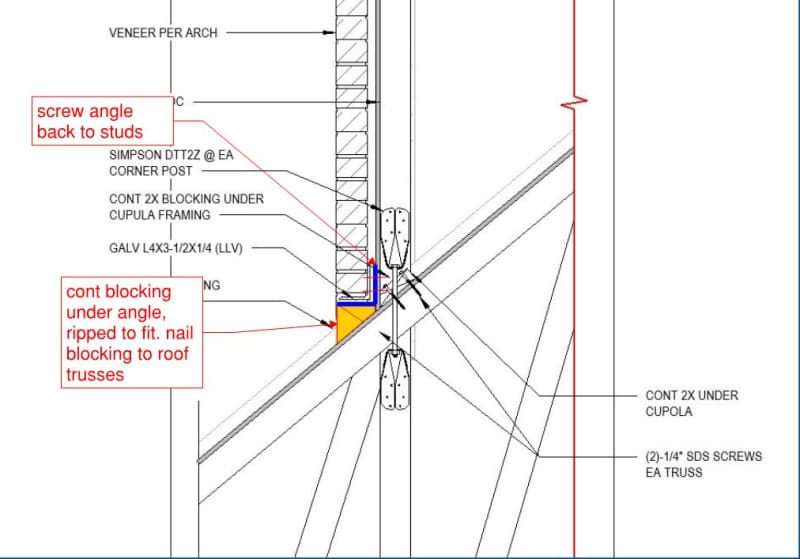
For the other direction, I'm planning to follow the IRC provisions and weld tabs to the angle.