I've been a long-time lurker on these forums, and have learned a LOT from you all over the years. I've come across this problem a number of times and have thoroughly stumped the other designers I work with, so thought I'd query The Brain Trust.
I have a pretty simple corner between three 90-degree planar faces with three G2 Styled Blends (5-degree single-patch) and a G2 Bridge Curve (modeled as a Law Extension so I could export a parasolid). I would like to fill that hole with another G2 surface.
Mesh Surface and Studio Surface both produce high patch-count surfaces that bulge out and cause issues trimming the planar-solid. The Sweep tools don't provide any tangent or curvature continuity. My best effort yet has been to create the single-patch using a G0 Mesh Surface, use Match Edge to control the continuity to "the corner" Blend, and use X-Form to manually move poles into the correct position. Here my personal favorite tip comes into play; sticking a post-it note to my monitor as a straight edge.
Alternately I can extract Point Sets using B-Surface poles, create Lines and Planes, and manually create the surface I want using Surface From Poles. This creates the perfect version of the surface above, but it's non-associative which goes against our modeling best-practice.
So the question is; is there an associative tool which will create this corner, G2, single-patch?
I have a pretty simple corner between three 90-degree planar faces with three G2 Styled Blends (5-degree single-patch) and a G2 Bridge Curve (modeled as a Law Extension so I could export a parasolid). I would like to fill that hole with another G2 surface.
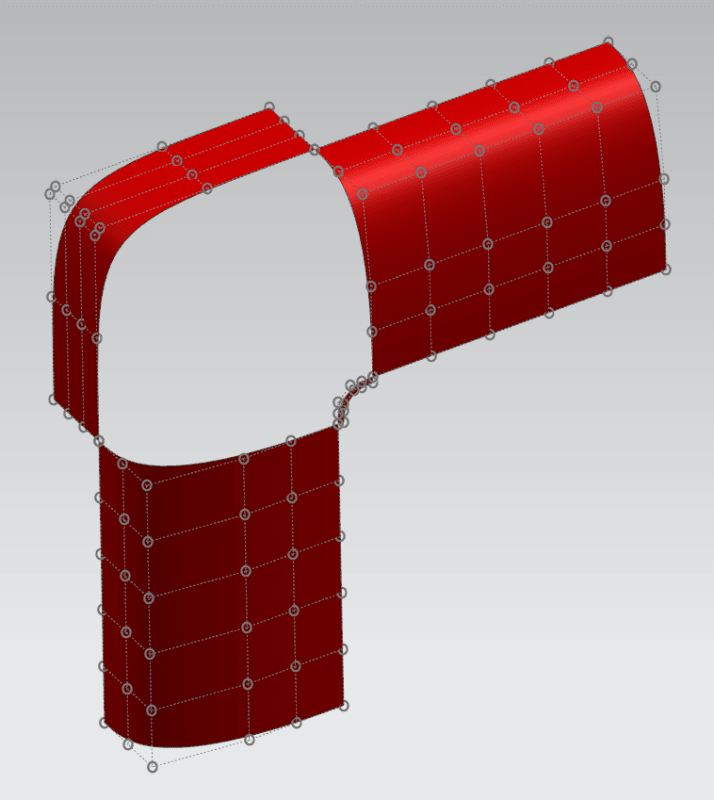
Mesh Surface and Studio Surface both produce high patch-count surfaces that bulge out and cause issues trimming the planar-solid. The Sweep tools don't provide any tangent or curvature continuity. My best effort yet has been to create the single-patch using a G0 Mesh Surface, use Match Edge to control the continuity to "the corner" Blend, and use X-Form to manually move poles into the correct position. Here my personal favorite tip comes into play; sticking a post-it note to my monitor as a straight edge.
Alternately I can extract Point Sets using B-Surface poles, create Lines and Planes, and manually create the surface I want using Surface From Poles. This creates the perfect version of the surface above, but it's non-associative which goes against our modeling best-practice.

So the question is; is there an associative tool which will create this corner, G2, single-patch?