SteelPE
Structural
- Mar 9, 2006
- 2,759
I am in the process of designing an addition for a client (a large industrial manufacturer). The project is the 5th project I have done for the client in the past 4 years. The existing structure is a series of 9 metal buildings that have been constructed over the years. The last 5 additions we have done have all utilized conventional framing (a total of 14 building placed on a site if you are trying to keep track).
Somewhere along the addition process (around the 7th structure) the client decided to make his building 2 stories. The client uses forklifts inside of his building to move material around inside the building and the existing suspended floor (4” slab on form deck with open web steel joists at 2’-0” oc.) has deteriorated badly. Buildings #8 on have used a tighter joists spacing with a thicker slab which has fared quite well (no observed damage). Attached you will find pictures of the existing slab.
The latest project will empty the building with the damaged slab and allow for repair. The area is to be repurposed with everything on the table (prohibiting access to forklift trucks, lowering the capacity of the floor for strengthening etc). I have suggested the following:
-placing steel plates on the floor to distribute the loads to the joists
-taking up the slab and casting a thicker slab in the area
-eliminating forklift trucks from the building, remove damaged slab areas and recast a new 4” thick slab
I am wondering if anyone might have any other options to help resolve this problem.
Somewhere along the addition process (around the 7th structure) the client decided to make his building 2 stories. The client uses forklifts inside of his building to move material around inside the building and the existing suspended floor (4” slab on form deck with open web steel joists at 2’-0” oc.) has deteriorated badly. Buildings #8 on have used a tighter joists spacing with a thicker slab which has fared quite well (no observed damage). Attached you will find pictures of the existing slab.
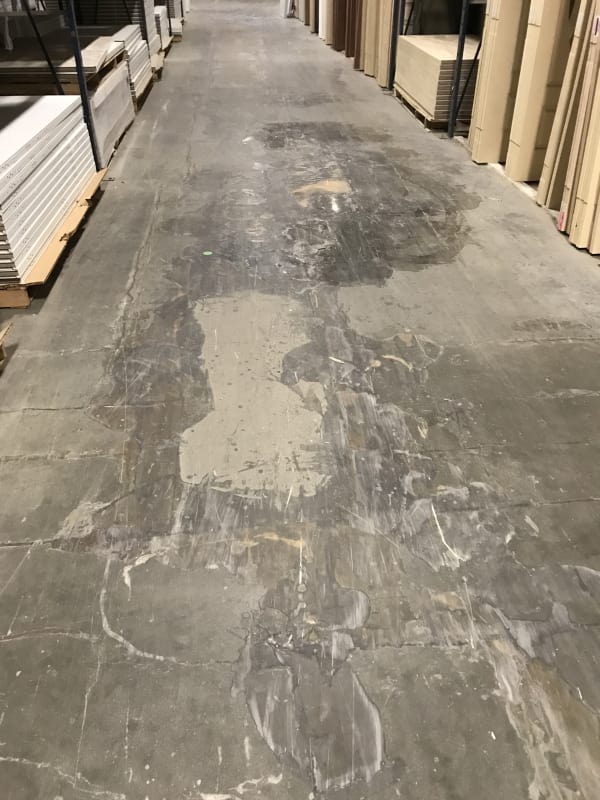
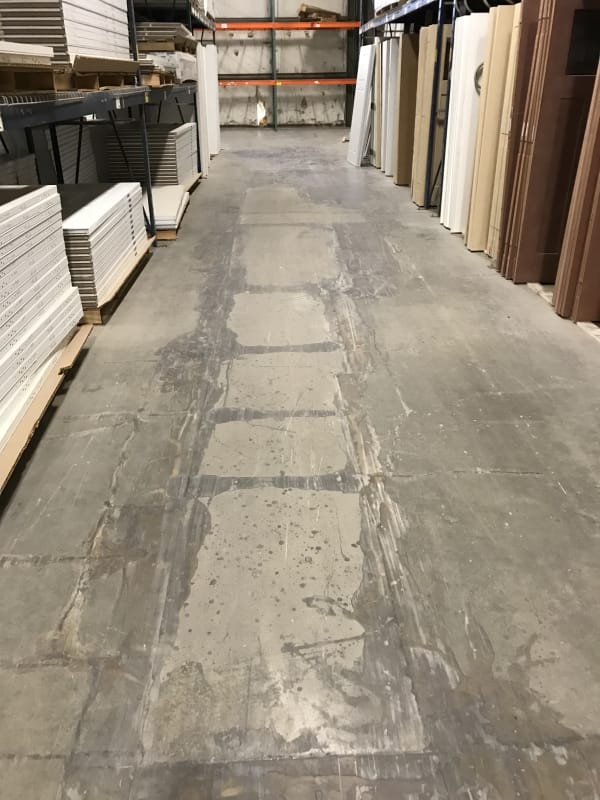
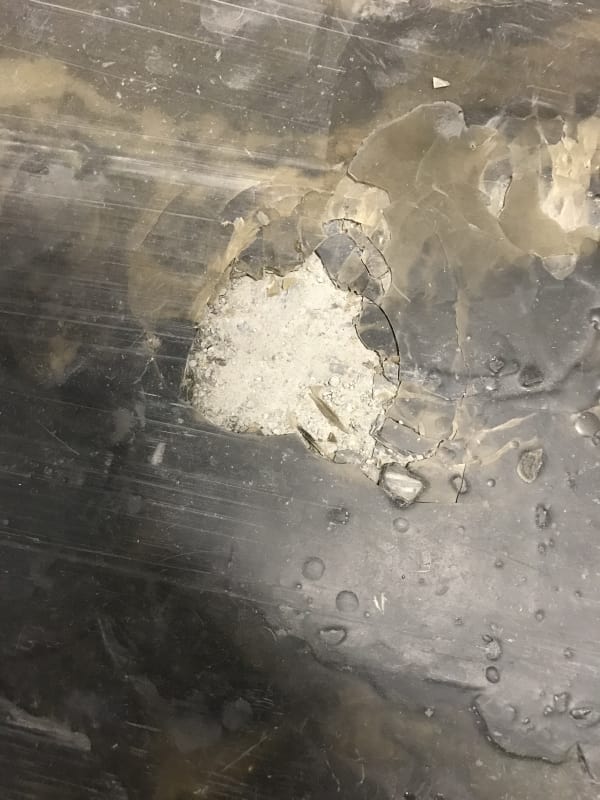
The latest project will empty the building with the damaged slab and allow for repair. The area is to be repurposed with everything on the table (prohibiting access to forklift trucks, lowering the capacity of the floor for strengthening etc). I have suggested the following:
-placing steel plates on the floor to distribute the loads to the joists
-taking up the slab and casting a thicker slab in the area
-eliminating forklift trucks from the building, remove damaged slab areas and recast a new 4” thick slab
I am wondering if anyone might have any other options to help resolve this problem.