SORJM
Computer
- Apr 5, 2016
- 30
I want to join the following two connected curves by the help of 6 Guides displayed in the image to create a solid Body.
I am using NX 10. In swept tool I can use only 3 guides.
Please tell the suitable way to form such type of solid using more than 3 guides.
I am a new user of the software so post your reply in detail so I can understand easily.
I am using NX 10. In swept tool I can use only 3 guides.
Please tell the suitable way to form such type of solid using more than 3 guides.
I am a new user of the software so post your reply in detail so I can understand easily.
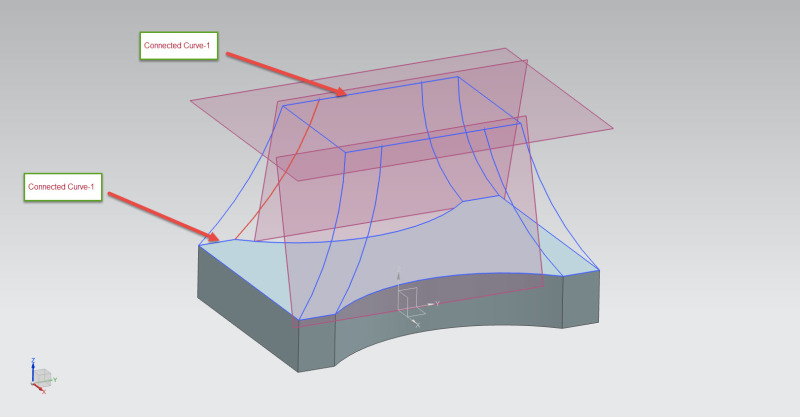